آهن اسفنجی یکی از محصولات پایه است که برای ساخت مقاطع فولادی مورد استفاده قرار میگیرد. در این مقاله میخواهیم به بررسی و ارزیابی روشهای مختلف تولید آهن اسفنجی بپردازیم. برای مطالعه عناوین زیر همراه ما باشید:
- آهن اسفنجی چیست؟
- کاربرد آهن اسفنجی
- روشهای تولید آهن اسفنجی
آهن اسفنجی چیست ؟
آهن اسفنجی چیست؟ ماده اولیه برای ساخت آهن و فولاد است که از بازیافت کانی آهن به صورت طبیعی یا فرآوری شده ساخته میشود. برای ساخت اهن اسفنجی گندله سنگ آهن که عیار ۶۷ درصدی دارد، پس از احیا موجب تولید آهن اسفنجی با متالیزاسیون fe ۹۲ درجه خواهد شد. محصول احیا شده بدون خنک شدن کوره با دمای ۶۰۰ درجه سانتی گراد به بخش فولادسازی منتقل میشود.
پس از ذوب و احیا در فولادسازی، آهن اسفنجی در فرایند ریخته گری به شکل دلخواه درخواهد آمد. اسلب، بیلت و میلگرد از مقاطع فولادی هستند که از آهن اسفنجی ساخته میشوند.
۵درصد از کل فولاد جهان از اهن اسفنجی ساخته میشوند که روز به روز به این مقادیر افزوده میگردد. به طور کلی آهن اسفنجی به طور مستقیم از سنگ آهن بدست آمده که به اصطلاح به آن DRI میگویند.
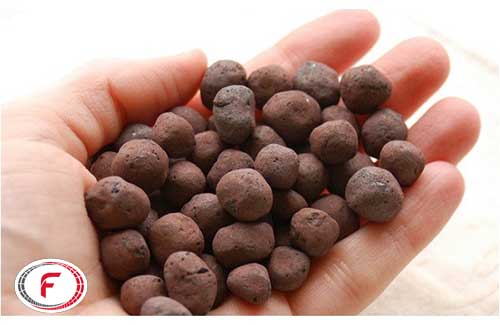
کاربرد آهن اسفنجی
یکی از مهمترین کاربردهای آهن اسفنجی، استفاده از آن در کورههای القائی است. در واقع این محصول پایه قادر است تا ۵۰ درصد جایگزین قراضه در کوره القایی شود. البته میزان و نحوه استفاده از آنها به دانش فنی و تجربه نیاز دارد. استفاده از آهن اسفنجی تحولی بزرگ در صنعت فولاد است. مزیت استفاده از آن، سازگاری با تمام روشهای تولید فولاد است. واحدهای بزرگ و کوچک صنعتی از این روش برای تولید محصولات خود استفاده میکنند. ایران به دلیل داشتن منابع طبیعی فراوان برای احیای مستقیم با مانعی مواجه نخواهد بود. آهن اسفنجی میتواند گزینه مناسبی به عنوان جایگزین ضایعات باشد. از همین رو میتوان آهن اسفنجی را جایگزین ضایعات نمود و ذوب مورد نیاز واحدهای فولادسازی را تامین نمود.
با استفاده از منابع گازی یا زغالسنگ احیای مستقیم سنگ آهن انجام میشود. محل قرار گرفتن کارخانه تولیدکننده به روش احیای مستقیم سنگ آهن بستگی دارد. به طور مثال کشور ایران به دلیل دسترسی به منابع گازی بالا، از گاز به عنوان منبع تولید آهن اسفنجی استفاده میکند. استفاده از زغالسنگ به عنوان منبع موجب بروز مشکلاتی از قبیل آلودگی هوا خواهد شد. از طرفی دسترسی به معادن زغالسنگ و تامین آن کار آسانی نیست. در حال حاضر هند بزرگترین تولید کننده آهن اسفنجی در دنیاست و از زغالسنگ به عنوان منبع استفاده میکنند.
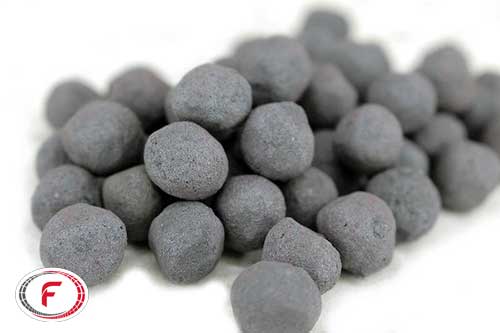
روشهای تولید آهن اسفنجی
فرایند میدرکس
در سال ۱۹۶۹ در شهر پرتلند ایالت ارگون آمریکا اولین واحد احیا مستقیم ایجاد شد. این واحد از دو کوره عمودی با قطر داخلی ۳.۷ متر ساخته شده بود که میتوانست در سال ۱۵۰ هزار تن آهن اسفنجی تولید نماید. با گذشت زمان و افزایش نیاز به آهن و فولاد در صنایع مختلف، فولادسازی با کیفیت بالا و قیمت مناسبتری انجام شد. شرکت میدرکس با گذشت زمان واحدهای بزرگتری را احداث نمود و کورههای عمودی میدرکس با قطر داخلی ۳.۷ متر به ۴.۲۵ و نهایتا ۷.۵ متر تولید شد.
مراحل تولید
الف) سنگ آهن ورودی: سنگ آهن ورودی در این فرایند به شکل گندله پخته شده است و از کلوخه سنگ آهن هماتیتی با عیار بالا و شرایط مناسب نیز میتوان با توجه به شرایط آن استفاده نمود.
ب) عامل احیاء کننده: در این فرآیند پس از فرآیند ریفرمینگ گاز طبیعی شکسته خواهد شد. لازم بذکر است که در این فرآیند، گاز منو اکسید کربن نسبت به هیدروژن سهم بیشتری دارد.
ج) نوع کوره احیاء و شرایط آن: کوره میدرکس تحت فشاری کمتر از اتمسفر کار میکند و وروزدی و خروجی آن دینامیکی و قابل تنظیم است.
د) درجه حرارت احیاء: حدود ۸۵۰ تا ۹۲۰ درجه سانتیگراد
ه) سابقه فرآیند: از حدود سال ۱۹۶۹
و) موقعیت فرآیند: کاملا تثبیت شده و تجاری
ز) ظرفیت فرآیند: در ابتدا ابعاد کوره میدرکس کوچکتر بود و در قطر کمتری ساخته شده بود. اما با گذشت زمان قطر آن بزرگتر و ظرفیت آنها بیشتر شد.
ح) سهم بازار: حدود ۶۰% کل تولید آهن اسفنجی
فرآیند HYL(نسل چهارم) یا Energiron
الف) سنگ آهن ورودی: در این فرآیند سنگ آهن به شکل گندله وارد کوره و پخته خواهد شد. استفاده از کلوخه سنگ آهن هماتیتی نیز در حد قابل قبول بلامانع است.
ب) عامل احیاء کننده: در این روش نیز همچون میدرکس از گاز طبیعی شکسته شده برای احیا استفاده مکنند. میزان هیدروژن در مخلوط گاز احیایی بیشتر از مونواکسید کربن است. در این روش هیدروژن به عنوان عامل اصلی احیا کننده خواهد بود.
ج) نوع کوره احیاء و شرایط آن: کوره در این روش نیز همچون روش میدرکس به صورت سافت عمودی است. قادر به تحمل فشار محیط تا ۷ اتمسفر بوده تا سرعت واکنش احیا بدست آید.
د) درجه حرارت احیاء: حدود ۸۵۰ تا ۸۷۰ درجه سانتیگراد
ه) سابقه فرآیند: از حدود سال ۲۰۰۳
و) موقعیت فرآیند: تثبیت نشده ولی تجاری
ز) ظرفیت: ظرفیت کورههای نسل چهارم قابل تنظیم است.
ح) سهم بازار: فعلا در حد ۴ مدول راه اندازی شده و یا در دست ساخت ميباشد.
فرآیند SL/RN ومشابه
الف) سنگ آهن ورودی: در فرآیند میدرکس از گندله پخته شده با کیفیت و ۳۰ درصد کلوخه سنگ آهن استفاده میشود. در این فرآیند میتوان استفاده از کلوخه را تا ۱۰۰ درصد افزایش داد. از طرفی استفاده از گندله خام نیز مشکلی ایجاد نخواهد کرد. سنگ آهن کلوخه هماتیتی باید با عیار بالا باشد و سنگ مگنتیتی برای انجام آن مناسب نخواهد بود.
ب) عامل احیاء کننده: در این روش میتوان ار زغالسنگ حرارتی به عنوان ماده احیا کننده استفاده نمود. مزیت آن نسبت به دیگر روشها این است که نیازی به استفاده از زغالسنگ با کیفیت بالا نخواهد بود. پس از قرار گرفتن زغالسنگ در کوره گاز مونواکسید تولید خواهد شد که این امر اکسید آهن را احیا خواهد کرد. علارغم حرارت بالای کوره، سرعت واکنش نسبتا پایین است. در این فرآیند گاز هیدروژن وجود ندارد.
ج) نوع کوره احیاء: کوره افقی Rotary Kiln به صورت دوار عمل میکند. فشار قابل تحمل برای این کوره کمی بالاتر از فشار اتمسفر است. کوره دوار از دو قسمت پیشگرم و منطقه احیا تشکیل شده است. گازهای خارج شده از کوره ۱۰۰۰ درجه سانتی گراد دما دارد. از همین رو برای تولید برق کاربرد دارند.
د) درجه حرارت احیاء: حدود ۱۰۰۰ تا ۱۱۰۰ درجه سانتیگراد
ه) سابقه فرآیند: از حدود سال ۱۹۸۰
و) موقعیت فرآیند: تثبیت شده و تجاری
ز) ظرفیت بهینه: حدود ۱۰۰ تا ۱۵۰ هزار تن به ازاء هر مدول
ح) سهم بازار: جمعا حدود از ۲۳% کل تولید آهن اسفنجی
فرآیند کوره تونلی
الف) سنگ آهن ورودی: سنگ آهن هماتیت یا مگنتیت به صورت نرمه با عیارهای ترجیحا بالا مثل ۶۵%.
ب) عامل احیاء کننده: مزیت این روش امکان استفاده از ذغال سنگ حرارتی با کیفیت نسبتا پایین به عنوان ماده احیاء کننده است.
ج) نوع کوره احیاء: کوره تونلی. کوره تونلی شامل سه بخش پیشگرم، منطقه احیاء و خنک سازی است.
د) درجه حرارت احیاء: حدود ۱۲۰۰ تا ۱۲۵۰ درجه سانتیگراد
ه) سابقه فرآیند: از حدود سال ۱۹۰۸
و) موقعیت فرآیند: تثبیت شده و تجاری
ز) ظرفیت بهینه: حدود ۵۰ هزار تن به ازاء هر مادول
ح) سهم بازار: جمعا حدود ۵% کل تولید آهن اسفنجی
منبع تامین محتوا فولاد۲۴