در حال حاضر، متالورژی پودر بیشتر در مواردی مورد استفاده قرار می گیرد که در ساختن محصولاتی با کیفیت عالی از مواد مناسب، تقریباً استفاده از کلیه روش های دیگر غیر ممکن باشد. البته در مواردی مثل ساختن رشته های مقاوم تنگستنی لامپ که روش هایی نظیر تراشکاری، کشیدن سیم و یا نورد غیر قابل استفاده اند، منحصراً از روش متالورژی پودر استفاده می گردد. در این مقاله عناوین زیر را با یکدیگر بررسی می کنیم تا به مفهموم کلی متالورژی پودر و دسته بندی آن ها آشنا شویم:
- تاریخچه متالورژی پودر
- مفهوم متالورژی پودر
- مراحل تولید و ساخت قطعات در متالورژی پودر
- مزایا و معایب متالورژی پودر
- محصولات و قطعات تولیدی با متالورژی پودر
تاریخچه متالورژی پودر
با این که ظاهراٌ در ۳۰۰۰ سال پیش از میلاد مسیح، یا استفاده از دانه های آهن اسفنجی نوع بسیار ابتدایی متالورژی پودر در مصر باستان وجود داشته است، لیکن تولید انبوه فرآورده های متالورژی پودر تا اواسط یا اواخر قرن نوزدهم آغاز نشد. در اوایل قرن بیستم، فرآیند گردفلز کاری برای تولید سکه و مدال های مسی، شمش های پلاتین و سیم های تنگستنی که ماده اصلی فیلامان لامپ روشنایی بودند، به کار می رفت. در سال های دهه ی ۱۹۲۰ نوک های تراش از جنس کاربید تنگستن و بوش های غیر آهنی تولید می شدند. یاتاقان های خود روغن کار و فیلترهای فلزی از دیگر محصولات اولیه بودند. در یک دوره پس از جنگ جهانی دوم، عامل پیشرفت و گسترش سریع این صنعت تولید قطعات مختلف اتومبیل بوده است که طی آن آهن و فولاد جایگزین مس به عنوان ماده پر مصرف تر متالورژی پودر شدند.
دیگر پیشرفت های دهه ی ۱۹۸۰ تولید تجاری پودرهای بی شکل ( غیر بلورین ) و انجماد سریع و تکامل تکنولوژی قالب گیری تزریقی بوده است. سال های اخیر دوران گسترش سریع صنعت متالورژی پودر بوده است، به طوری که در فاصله سال های ۱۹۶۰ تا ۱۹۸۰ مصرف پودر آهن ده برابر شده است و این رشد سریع همچنان ادامه دارد سرانجام در سال ۱۹۹۰ در یک اتومبیل متوسط آمریکائی حدود ۲۱ پوند ( ۱۰ کیلوگرم ) قطعه متالورژی پودر وجود داشت. در سال ۱۹۹۲ این رقم به ۲۶ پوند افزایش یافت، و در سال ۱۹۹۵ اتومبیل های جدید بیشتر از ۳۰ پوند ( ۱۳.۶ کیلوگرم ) قطعه متالورژی پودر در خود داشتند. فولاد زنگ نزن، فولادهای پرآلیاژ، آلومینیوم، و پودرهای مس از مواد پرمصرف در این صنعت می باشد. برخی از قطعات اولیه صنعت متالورژی پودر در شکل زیر آورده شده است.
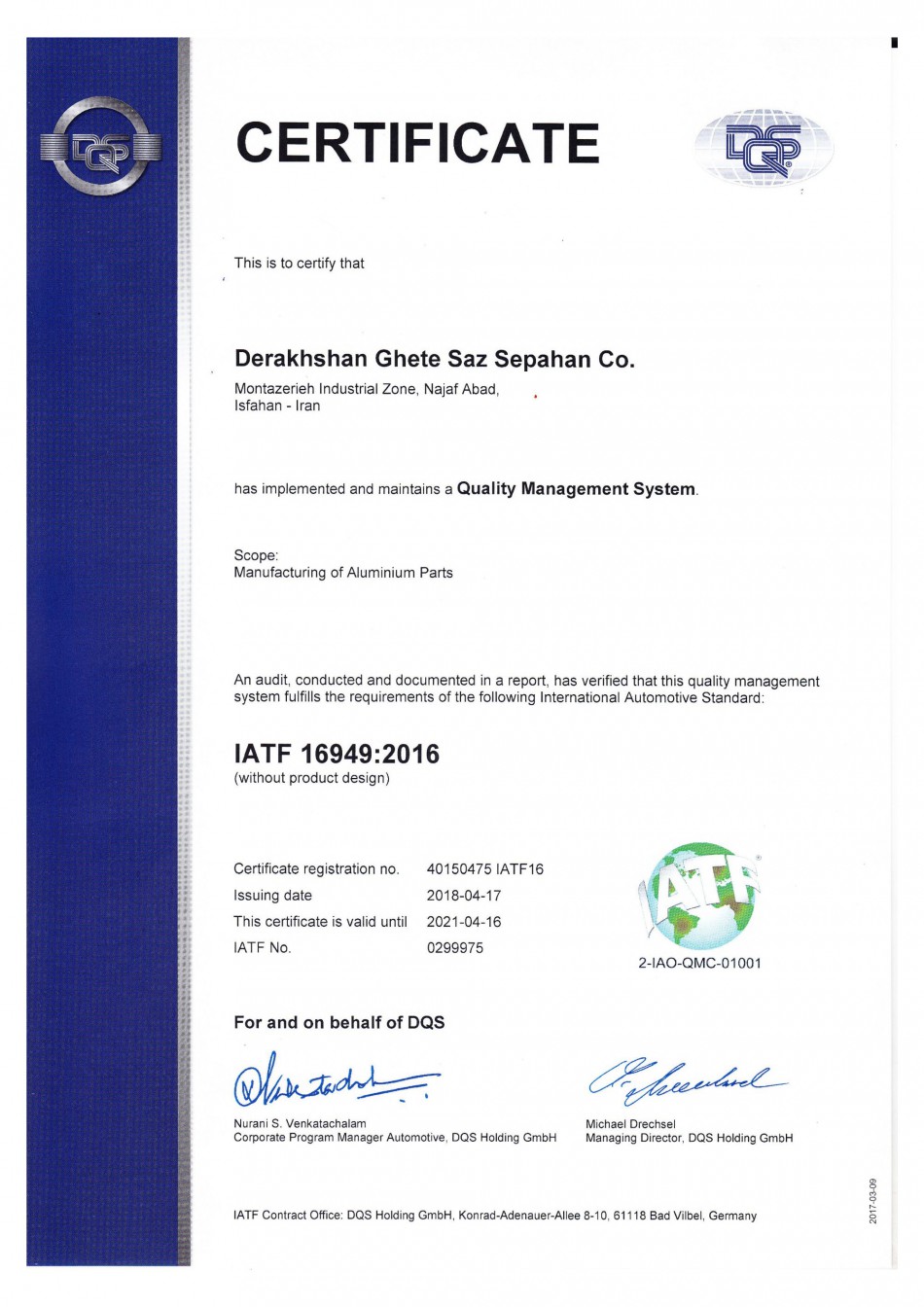
مفهوم متالورژی پودر
متالورژی پودر فرایند قالبگیری قطعات فلزی از پودهای فلزی توسط اعمال فشارهای بالا برای دقیق دشن اشکال می باشد. پس از عمل تراکم پودرهای فلزی، عمل سینتر کردن در دمای بالا در یک کوره با اتمسفر کنترل شده انجام می شود که در آن فلز متراکم جوش خورده در حالت سرد به صورت ساختمان همگن محکمی پیوند می خورد .خواص فیزیکی ماده متراکم سینتر شده شبیه به خواص فلز سازنده اصلی است. عمل سینتر کردن معمولاٌ در حدود ۸۰ در صد نقطه ذوب سازنده اصلی انجام می گیرد تا امکان چسبیدن ذره ها در امتداد فصل مشترک ذره های پودر وجود داشته باشد. تراکم فلزات پودر شده در حدیده بوسیله پرس کردن همزمان با سنبه های بالائی و پائینی تحت فشارهای حدود ۳۰ تن در اینچ مربع روی آن پرس می کنند. از جمله قطعات نمونه ای که بوسیله این فرآیند تولید می شوند می توان ابزار برش، اجزاء ماشین، قطعات اتومبیل، یاتاقانهای خود روغن کار، فیلترهای متخلخل و مواد مغناطیسی را نام برد.
محصولات فرآيند متالوژي پودر را مي توان به پنج دسته كلي تقسيم كرد:
- قطعات متخلخل با درصد تخلخل قابل كنترل مانند فيلترها.
- قطعاتي كه اشكال پيچيده دارند و توليد آنها به روشهاي ديگر مستلزم ماشين كاري بسيار زياد است.
- محصولاتي كه ماشين كاري آنها مشكل است و يا داراي جنس سخت هستند.
- محصولاتي كه بنا به ايجاب شرايط خواص مشخصه چند ماده را داشته باشند.
- توليداتي كه در آنها از فرآيند متالوژي پودر براي ايجاد خواص مكانيكي بهتر استفاده مي گردد.
مراحل تولید و ساخت قطعات در متالورژی پودر
مراحل تولید و ساخت قطعات با استفاده از متالورژی پودر را می توان در چهار مرحله زیر خلاصه کرد:
- تولید پودر
- مخلوط کردن پودر
- متراکم کردن و شکل دهی پودر
- تف جوشی یا زینترینگ
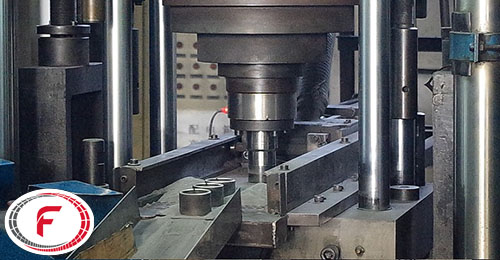
تولید پودر فلزات
پودر فلزی را می توان ذرات فلزی یا آلیاژی با اندازه یک تا هزار میکرون تعریف کرد. این ذرات ممکن است به صورت کروی، ورقه ای و یا شکل های بی قاعده باشد. در زمان های گذشته، پودرهای فلزاتی مثل طلا و مس با روش های ابتدایی مانند سوهان کاری تهیه می شد و در کاربردهای تزییناتی مثل ساخت رنگ ها و سرامیک ها به کار می رفت. با پیدایش فرایند متالورژی پودر و گسترش سریع آن، نیاز به پودرهای فلزی نیز به سرعت افزایش یافت و روش های مختلفی برای تولید پودر ابداع گردید. روش های تولید پودر فلزات را می توان به سه گروه عمده زیر دسته بندی نمود:
- روش های مکانیکی
- روش های شیمیایی
- روش های فیزیکی
مخلوط کردن پودر
پس از آن که پودرهای فلزی آماده شد، آن ها را درجه بندی کرده و به همراه مواد افزودنی با هم مخلوط می کنند. این عمل کار مهم و دقیقی است، چرا که یکنواختی مخلوط در کیفیت محصول تولید شده تاثیر زیادی دارد.
متراکم کردن و شکل دهی پودرهای فلزات
یکی از مهم ترین مراحل تولید در متالورژی پودر، وارد کردن فشار یا پرس کردن پودر و دستیابی به شکل مورد نظر است. در حین فشردن، ذرات پودر فلزی به یکدیگر کاملاً نزدیک می شوند. بدیهی است که در اثر تراکم و نزدیک شدن ذرات به یکدیگر، سطح تماس آن ها افزایش می یابد و به این ترتیب محصولی فشرده تولید می شود که البته محصولی تمام شده نیست و باید فرایند زینترینگ نیز بر روی آن انجام شود. از ویژگی های مورد نظر در این مرحله، علاوه بر دستیابی به شکل معین، رسیدن به دانسیته کافی و همچنین یکنواختی دانسیته در تمام قطعه، استحکام کافی برای حمل و نقل و سالم بودن قطعه (بدون ترک خوردگی و یا امواج سطحی) است. لازم به ذکر است که با اعمال فشارهای بالا به ذرات پودر، تغییر شکل پلاستیکی در ذرات شروع شده و بخش های نازک پودر خم می شوند و یا می شکنند. در نهایت اعمال فشار موجب مقداری جوش سرد در بین ذرات پودر می شود. شکل دادن به پودر روش های مختلفی دارد که به چند مورد از آن ها اشاره می کنیم:
- فشردن یک طرفه
- فشردن دوطرفه
- فشردن ایزواستاتیک
- آهنگری پودر
- نورد پودر
- تزریق پودر
- فشردن داغ
- اکستروژن داغ
- شکل دهی پودرهای فلزی به روش تخلیه ولتاژ بالا
تف جوشی (زینترینگ)
پودر را به طریقی که تشریح شد، تولید و شکل می دهند. اما قطعه خام به علت سست بودن پیوند بین ذرات (ذرات پودر در مرحله پرس کردن فقط به یکدیگر اتصال مکانیکی پیدا می کنند)، قادر نیست که تنش های کاری را تحمل کند، در نتیجه می شکند. برای این که قطعه بتواند تنشهای کاری را تحمل کند، لازم است که پیوند قوی تری بین ذرات به وجود آید. تف جوشی یا زینترینگ فرایندی است که این پیوند را برقرار می کند. در اثر این عملیات، تحرک اتم ها زیاد شده، امکان از بین رفتن مناطق پر انرژی فراهم می آید. مناطق پر انرژی، فصل مشترک های بین ذرات است که قاعدتاً اتصال نقطه ای بین ذرات برقرار کرده اند. با از بین رفتن این مناطق، گوشه های تیز به صورت گرد و منحنی شکل در می آید. حجم حفره ها کاهش می یابد. نوع اتصال از حالت مکانیکی به اتصال اتمی تبدیل می شود و سطح تماس بین ذرات افزایش می یابد. در اثر این اتفاقات، حجم قطعه کاهش می یابد ولی در عوض، دانسیته و استحکام آن افزایش می یابد.
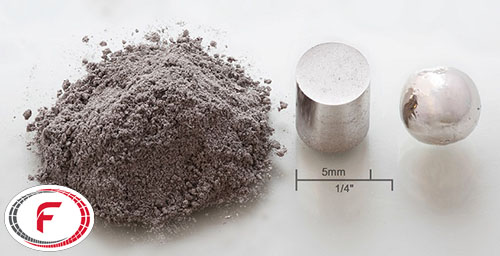
مزایا و معایب متالورژی پودر
- در مقایسه با دیگر فرآیند های شکل دهی فلزات متالورژی پودر از نظر مصرف مواد و انرژی بصرفه می باشد.
- متالورژی پودر برای ساخت قطعات با شکل پیچیده از نظر هزینه ها بصرفه است.
- نیاز به ماشینکاری را به حداقل می رساند.
- گستره وسیعی از مواد مهندسی قابل استفاده می باشد.
- با انتخاب مناسب فرایند و مواد، توسعه ریزساختار مورد نیاز در ماده قابل دستیابی خواهد بود. قطعات متالورژی پودر دارای سطح نهائی خوبی هستند. حتی ممکن است برای بهبود استحکام و یا مقاومت به سایش عملیات حرارتی شوند.
- متالورژی پودر دارای قابلیت تولید مجدد قطعه به قطعه می باشد.
- برای تولید با تیراژ متوسط و بالا مناسب می باشد.
- در مواقع ضروری ایجاد ریز تخلخل های کنترل شده برای فیلتراسیون و ایجاد قابلیت خود روانکاری قابل دستیابی است.
- دقت ابعادی خوب است اما در حد قطعات ماشینکاری شده نمی باشد.
- در مورد قطعات متالورژی پودر آهنی، دارای چکشخواری ductility کمتر و مقاومت به ضربه کمتر نسبت به فولاد های کار شده می باشند.
- بیشتر قطعات ساخته شده با فرایند متالورژی پودر متخلخل هستند. و این مسئله باید در انجام فرآیندهای تکمیلی مورد توجه قرار گیرد.
محصولات و قطعات تولیدی با متالورژی پودر
از جمله محصولات و قطعاتی که با روش متالورژی پودر تولید می شوند، می توان موارد زیر را نام برد:
- رشته های نازک مقاومت و الکترودهایی که در لامپ مشاهده می شوند.
- لوله های تولید اشعه X که تماماً از جنس فلزاتی نظیر تنگستن، مولیبدن و تانتالن می باشند.
- ابزارهای ساخته شده از سرمت (cermet) که کامپوزیتی با فاز غالب سرامیک و جزء فلزی همراه با آن است و در سال های اخیر تولید آن ها به روش متالورژی پودر توسعه چشمگیری داشته است و در کارهای ماشینی تغییرات اساسی ایجاد کرده اند، به طوری که سرعت برش با آن ها ۱۰ برابر قبل افزایش یافته است.
- مته ها و ابزارهای حفاری که از جنس فلزات سخت می باشند و میزان حفاری را در چاه های نفت و گاز و نیز هم چنین در معادن فوق العاده افزایش داده اند.
- علاوه بر ابزارهای برش، تکنیک متالورژی پودر قادر است ابزارهای سوراخ کننده، حدیده های کشش سیم و وسایل مشابه دیگر را نیز تولید کند.
تهیه شده در گروه تولید محتوای فولاد ۲۴