فورج چیست؟
در روش فورج، قطعهی اولیه که لقمه نامیده میشود در میان دو نیمهی قالب قرار میگیرد و نیرویی زیاد به صورت آرام و گاهی ضربهای به آن وارد میشود. به این ترتیب قطعهی گداخته در محیط قالب، شکل و فرم داخل قالب را به خود میگیرد و فلز اضافی به حفرهی فلاش وارد میشود که بعداً از قطعه جدا شده و دور ریز قطعهی فورج شده محسوب میگردد.
پروسهی فورج معمولا به صورت گرم انجام میشود. هر فلزی میزان حرارت مشخصی برای فورج شدن دارد. اکثر فلزات، قابلیت آهنگری و فورج شدن را دارا هستند. فلزاتی مانند فولادهای آلیاژی، فولادهای کربنی، آلومینیوم و آلیاژهای آن، برنج ،مس و آلیاژهای آن ها و... برای فورج مناسب هستند. قالبهای فورج برای فرم دهی و شکل دهی فلزات در تولید انبوه استفاده میشود که گاهی با حرارت دهی قطعات کار و گاهی بدون حرارت دهی صورت میگیرد.
فـورج کردن معمولاً توسط گرم کردن فولاد دور ریخته شده، فولاد مربع (متوسط، کوچک جعل) و یا شمش (جعل بزرگ) در درجه حرارت بالا انجام میشود. فـورج میتواند ساختار ریخته گری، نقاط ریخته گری (مانند انقباض، تخلخل و غیره)، ساختار قطعه قطعه، پالایش دانه، ترکیب یکنواخت و در کل خواص مکانیکی فلزات را بهبود ببخشد. بنابراین، عمدتاً برای حمل بار سنگین، بار متناوب، قطعات مکانیکی مانند چرخ و دنده ابزارهای مختلف، میل لنگ و میله اتصال موتور خودرو، قلابهای جرثقیل و ابزارهای مختلف برش، قالب و غیره استفاده میشود.
قالبهای فـورج برای فرم دهی و شکل دهی فلزات در تولید انبوه استفاده میشود که گاهی با حرارت دهی قطعات کار و گاهی بدون حرارت دهی صورت میگیرد. قالبهای فـورج به دو دسته تقسیم میشوند:
- قالبهای بسته فـورج (Impression Die forging)
- قالبهای باز فـورج (Open Die forging)
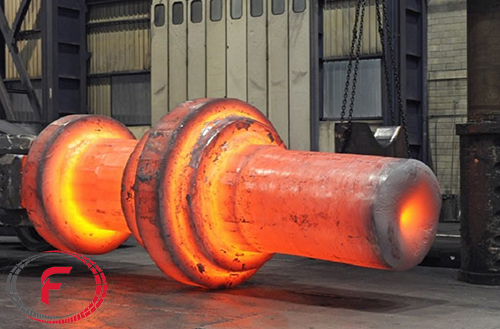
روش فـورج با قالب باز
در روش فـورج کاری سرد، عملیات تولیدی به صورت سرد انجام میگیرد که شامل خم کاری، کشش، کله زنی، نقش زنی، اکستروژن و پیچ زنی میباشد که در این روش به نیروی بالاتری نسبت به فـورج گرم احتیاج است. دقت ابعاد قطعات تولید شده با روش فـورج سرد، بیشتر میباشد.از این روش برای ساختن قطعات با اشکال، اندازه وجنسهای مختلف استفاده میشود. با این روش میتوان جریان فلز و ساختار دانههای آن را کنترل نمود و در نتیجه به استحکام و چقرمگی خوبی دست یافت. از این روش برای تولید قطعاتی که در شرایط کاری تنش بالا و بحرانی کار میکنند، استفاده میشود.
از قطعات معروفی که امروزه با استفاده از این روش تولید میشود میتوان به میل لنگ شاتون، دیسکهای توربینها، چرخ دندهها، چرخها و ابزار آلات اشاره نمود. فـورج را میتوان دردمای اتاق (فـورج سرد) یا در دماهای بالاتر(فـورج گرم و فـورج داغ بسته به دما) انجام داد.
در فـورج سرد به نیروهای فوق العاده بزرگی برای شکل دادن قطعه نیاز است و ماده خام بایستی به اندازه کافی قابلیت چکش خواری داشته باشد . اما قطعة تولید شده با این روش دارای سطح پایانی و دقت ابعادی خوبی است. در فـورج داغ به نیروی کمتری نیاز است ولی قطعات تولیدی با این روش دارای سطح پایانی و دقت ابعادی چندان خوبی نیستند. معمولاً قطعات تولیدی توسط فـورج به عملیات اضافی ( پایانی) جهت تبدیل شدن به قطعه مناسب کار و حصول دقت مطلوب نیاز دارند.
با استفاده از روش فـورج دقیق میتوان این عملیات را به حداقل رساند. قطعههایی که با استفاده از فـورج تولید میشود را نیز میتوان با سایر روشها نظیر ریخته گری، متالوژی پودر و ماشین کاری تولید نمود وهمانطور که انتظارمیرود هرکدام ازاین روشها دارای مزایا و محدودیتهای مربوط به خود از نظر استحکام، چقرمگی، دقت ابعادی سطح پایانی و نقصهای ساختاری هستند.
بازار آنلاین خرید و فروش محصولات فولادی
روش فـورج با قالب حفره دار و قالب بسته
در فـورج با قالب حفره دار قطعه خام توسط نیروهای فشاری پرس به شکل حفرههای قالب در میآید. توجه شود که مقداری از ماده بین دو نیمه قالب به صورت زائده باقی میماند. زائده نقش بسیار مهمی در جریان ماده در قالبهای حفره دار ایفا میکند. این زائده کوچک سریعاً خنک میشود و به سبب مقاومت اصطکاکی، ماده داخل حفرههای قالب را تحت فشار بالا قرار داده و باعث پر شدن کامل حفرههای قالب میشود.
مراحل شکل دهی بیلت در قالب حفره دار به این صورت است که مقداری از ماده اضافی به صورت زائده در بین دو نیمة قالب باقی میماند. بریده ماده خام (بلانک) ممکن است از فرایندهایی نظیر ریخته گری، متالورژی پودر، برشکاری و یا فـورج بدست آمده باشد. این بلانک روی نیمة پایینی قالب قرار گرفته و با پایین آمدن نیمه بالایی قالب به تدریج شکل میگیرد.
از فرایندهای شکل دهی نظیر باریک سازی و لبه زنی برای توزیع ماده به قسمتهای مختلف بلانک استفاده میشود. در باریک سازی، ماده از یک ناحیه به سمت بیرون حرکت کرده و در لبه زنی در یک ناحیه جمع میگردد. سپس قطعه توسط فرایند لقمه کاری و با استفاده از قالبهای لقمه زنی به صورت ظاهری شاتون درمیآید. در آخرین عملیات فـورج، قطعه توسط قالبهای حفره دار شکل نهایی را به خود میگیرد. در انتها، زائده برشکاری میشود.
انواع روشهای فـورج
- آهنگری سنتی و دستی (چکش و سندان)
- فـورج با پتک اتوماتیک بدون قالب
- فـورج قالب باز (open die forging)
- فـورج قالب بسته (closed die forging)
- فـورج غلطکی (Roll Forging)
- فـورج حلقه ای (Ring Forging)
- فـورج کله زنی و کلفت کاری (upsetting forging)
- فـورج با انرژی بالا (High Energy Rate Forging)
- فـورج هم دما (Isothermal Forging)
- فـورج شعاعی (radial forging)
- فـورج دورانی (orbital forging)
- فـورج متالورژی پودر (powder metallurgy Forged )
- فـورج دقیق (Precision Forging)
طراحی قالب های فـورج
طراحی قالبهای فـورج به دانش زیادی درباره خواص استحکام، چکش خواری، حساسیت به نرخ تغییرشکل و دما، اصطکاک و شکل قطعه نیاز دارد. اعوجاج قالب تحت بارهای بالاخصوصاً در تولید قطعات با تلرانس کم قابل ملاحظه میباشد. مهمترین قانون در طراحی قالب این است که قطعه در هنگام عملیات فـورج در جهتی که دارای کمترین مقاومت است جریان مییابد. بنابراین قطعه ( شکل میانی) بایستی به گونهای شکل داده شود تا تمامی حفره های قالب پر شود. در شکل دهی اولیه قطعه، ماده نباید به آسانی به سمت زائده حرکت کند. الگوی جریان دانهها بایستی مطلوب باشد و لغزشهای شدید بین قطعه و قالب بایستی به حداقل برسد تا فرسایش کاهش یابد. انتخاب اشکال نیازمند تجربه زیادی بوده و شامل محاسبات سطوح مقطع در هر موقعیتی از فـورج میباشد. از آنجایی که ماده در این فرایند تحت تغییر شکلهای مختلفی در مناطق مختلف حفرههای قالب میباشد، خواص مکانیکی بستگی به موقعیت فـورج دارد.
آهنگری سنتی و دستی(چکش و سندان)
مرسوم ترین و اولین روش ساخت قطعات با روش فـورج به روش سنتی بر میگردد که با دو ابزار ساده و در اصطلاح چکش و سندان انجام میشود. از مزایای این روش میتوان به نداشتن هزینه قالب و تولید قطعات با اشکال ساده ذکر کرد و همچنین بزرگترین عیب این روش این است که نیاز به اپراتور یا کارگر ماهر دارد.
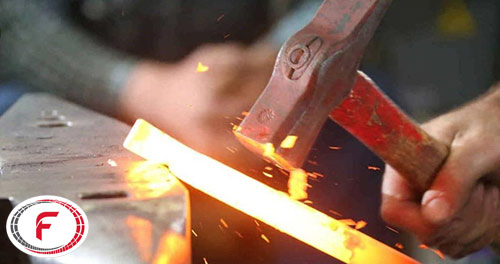
فـورج با پتک اتوماتیک بدون قالب
این روش برای ساخت قطعات بزرگ بر روی پرسهایی با دو سطح قالب صاف برای کم کردن قطر و افزایش طول مورد استفاده قرار میگیرد و این ضربات تا مواقعی ادامه پیدا خواهد کرد تا به اندازه مورد نظر برسیم.
فـورج غلتکی(Roll Forging)
روش فورج غلتکی معمولاً برای کاهش قطر یا ضخامت و افزایش طول مثل میلههایی با مقطع متغیر مورد استفاده قرار میگیرد. قالبهای مورد استفاده در این روش شامل انواع مختلفی چون تک غلتکی، دو غلتکی، سه غلتکی، گوهای مقعر و گوهای تخت میباشند.
فورج حلقهای(Ring Forging)
فورج حلقهای برای افزایش محیط حلقه از طریق کاهش سطح مقطع و با استفاده از دو غلتک چرخان انجام میشود. در این روش باید قطعه کار و بیلت اولیه طی فرایندی دارای سوراخی باشد تا بتوان با این روش به کاهش سطح مقطع و افزایش محیط حلقه پرداخت. برای افزایش محیطی قطعه از غلتک داخلی و برای کنترل ضخامت از دو غلتک مخروطی شکل استفاده میشود.
فورج کله زنی و کلفت کاری(upsetting forging)
کله زنی و کلفت کاری به عمل زیاد کردن قطر یک میله در انتها یا بخش میانی به وسیله اعمال فشار در جهت طولی آن گفته میشود. عمل کلفت کاری میتواند به صورت سرد یا گرم انجام شود.
فورج با انرژی بالا(High Energy Rate Forging)
فورج با انرژی بالا یعنی سرعت تغییر شکل زیاد در واحد زمان. این نوع تغییر شکل روی موارد زیر تأثیرگذار خواهد بود:
- دمای شکل دهی
- جریان فلز در جسم تغییر شکل یافته
- اصطکاک ایجاد شده در جدار قالب
- میزان تغییر شکل یا کرنش
- سرعت تغییر شکل یا نرخ کرنش
فورج هم دما(Isothermal Forging)
فورج هم دما در دماهای بالاتر از دمای تبلور مجدد قطعه انجام میشود و دمای قالب به دمای قطعه نزدیک است. در این فرایند معمولاً دمای قالب در محدوده دمای تبلور مجدد فولاد قالب است. جنس قالب های روش فورج هم دما از فولادهای آلیاژی با تنگستن زیاد است. اگر قالب و قطعه کار خـواص مکانیکی مشابه داشته باشند، باعث صدمه خوردن شکل حفره قالب خواهد شد.
فورج شعاعی (radial forging)
این فرایند از دو یا چند قالب که حرکت آنها به صورت شعاعی میباشد، تشکیل یافته است. معمولاً برای قطعات توپر یا لولهای از این روش استفاده میشود. معمولاً سوپر آلیاژهای دما بالا را میتوان با این روش شکل داد.
فورج دورانی (orbital forging)
در این روش نیمه بالایی قالب به حالت دورانی میچرخد و نیمه پایینی قالب به آهستگی به طرف نیمه بالایی قالب حرکت میکند تا حفره قالب کاملاً پر شود. البته در برخی موارد ممکن است قالب پایینی نیز دوران داشته باشد. قالب بالایی در این فرایند در امتداد محور ثابت است اما حول محور خودش حرکت مداری ایجاد میکند. این فرایند نسبتاً کم سر و صدا میباشد. دیسکها و قطعات مخروطی و پوششهای انتهای یاتاقانها از انواع قطعات تولید شده با این روش میباشد.
فورج متالورژی پودر (powder metallurgy Forged )
فورج متالوژی پودر ترکیبی از دو فرایند متالوژی پودر و فورج میباشد. اولین کاربرد متالورژی پودر برای تولید پلاتین با دانسیته کامل بود که در قرن ۱۹ میلادی صورت گرفت. چرا که در آن زمان امکان ذوب پلاتین به دلیل نقطه ذوب بالا وجود نداشت.
فورج دقیق (Precision Forging)
فورج دقیق فرایندی برای تولید قطعاتی با اندازه دقیق و نهایی میباشد. نکات و مواردی که در تولید قطعه با این روش مطرح است عبارت است از:
- اتلاف زمان
- اتلاف هزینه
- اتلاف انرژی
در روشهای دیگر مثل ماشین کاری، سنگزنی باعث شکستگی الیاف میشود و در نتیجه تنش کمتری را محصول نهایی نسبت به این روش تحمل میکند. این روش موارد گفته شده را حل میکند و استحکام بالا برای محصول تولیدی را دارا خواهد بود. این فرایند عمدتاً برای تولید انواع چرخ دنده استفاده میشود.
در ادامه با ما همراه باشید با فیلمی از فرایند فورج کردن:
تهیه شده در گروه تولید محتوای فولاد۲۴