تولید فولاد با محیط زیست رابطهی تنگاتنگی دارد. چند نکتهی بسیار مهم در مورد فولاد وجود دارد که ابتدا باید به آنها اشاره شود:
- فولاد آهنی است که بخش بسیاری از کربنش جدا شده است.
- آهن ۵ درصد از پوستهی کرهی زمین را در بر گرفته و چهارمین عنصر فراوان در سطح زمین است.
- ۹۸ درصد از آهن استخراج شدهی دنیا برای تولید فولاد استفاده میشود.
- فولاد ۹۵ درصد از تولید فلزات دنیا را تشکیل میدهد.
- بزرگترین تولید کنندگان فولاد در دنیا به ترتیب چین، اروپا، ژاپن، آمریکا و هند هستند.
- ۵۱ درصد از فولاد تولید شده در جهان برای ساختمان سازی استفاده میشود.
- ۶/۵ درصد از دی اکسید کربن جهان به واسطهی تولید فولاد ایجاد میشود.
همان طور که میبینید فولاد و طبیعت بسیار به هم وابسته هستند. میتوان این رابطه را در هشت مرحله بررسی کرد.
مرحلهی اول: استخراج از معدن
استخراج سنگ آهن شروع تولید فولاد است. آهن به صورت آزاد در طبیعت وجود ندارد زیرا بسیار واکنش پذیر است و با دیگر عناصر ترکیب شده و به صورت سنگ در میآید. سنگهایی که بیشترین مقدار آهن را دارند معمولاً در سطح زمین هستند و به راحتی استخراج میشوند.
دو نوع اصلی آهن استخراج شده نامهای هماتیت و مگنتیت دارند و بیشتر آنها در معادن باز هستند. سنگی برای استخراج به صرفه است که حداقل ۲۰ درصد از آن را آهن تشکیل داده باشد.
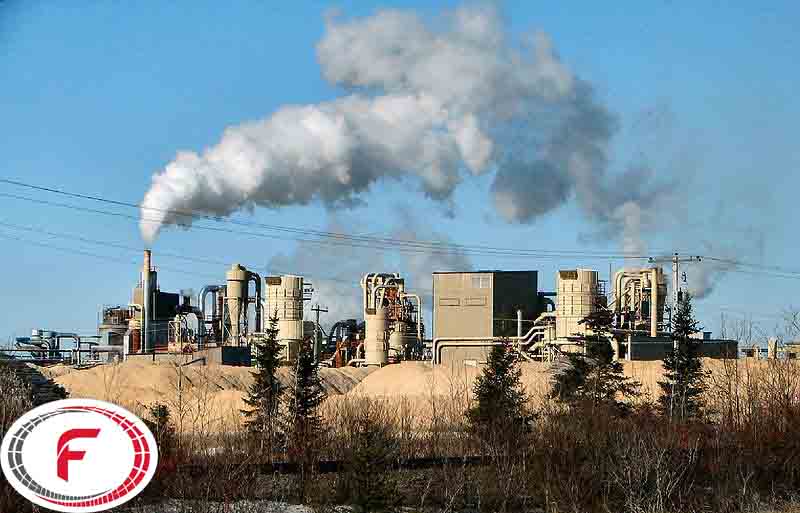
کجاها باید به دنبال سنگ آهن گشت؟
سه منبع بزرگ سنگ آهن در جهان به ترتیب چین با ۲۳%، استرالیا ۱۸%، و برزیل ۱۸% هستند. سنگ آهن به انواع مختلفی از آهن تبدیل میشود. معمولاً آن را به فرم آهن پیگ در میآورند. آهن پیگ از ۹۲ تا ۹۴ درصد آهن و ۳ تا ۵ درصد کربن تشکیل شده است. خود آهن پیگ استفادههای محدودی دارد و بیشتر آن برای تولید انواع فولاد راهی کارخانههای فولادسازی میشود. در این کارخانهها کربن آن حذف و برخی عناصر دیگر مثل نیکل و منگنز به آن اضافه میشود تا فولاد شکل بگیرد.
-سنگ آهک
سنگ آهک در واقع کربنات کلسیم است. از نظر زمین شناسی، سنگ آهک معمولاً به صورت رسوب پیدا میشود و به راحتی قابل جدا شدن است. این سنگ آهک استخراج شده برای تولید فولاد به کارخانهها فرستاده میشود.
-کُک
کک را از زغال سنگ میگیرند. به زغال سنگ آنقدر حرارت میدهند و آن را کربنیزه میکنند تا به کک تبدیل شود. بعد از این آن را از اجاق خارج کرده و خنک میکنند تا برای استفاده در کوره آماده باشد. گاز آزاد شده در فرآیند کربنیزه کردن نیز جمعآوری شده و از آن به عنوان سوخت استفاده میشود.
مرحلهی دوم: تولید آهن
کک، آهک و سنگ آهن وارد کوره میشوند. سنگ آهک هم در کنار آنها قرار میگیرد. گاز داغی از سمت کوره به قسمت پایین کوره وارد میشود. آهن موجود در سنگ آهن و آهک ذوب میشود و در قسمت پایینی کوره یک استخر از فلز مذاب را تشکیل میدهند. سنگ آهک با ناخالصیها سنگهای مذاب ترکیب میشود و مایعی را تشکیل میدهد که از آهن سبکتر است و روی استخر معلق میماند.
چُدن
آهن مذابی که در کف کوره جمع شده است میتواند به عنوان چدن مورد استفاده قرار بگیرد. چدن در حالت مذاب خیلی لغزنده است و پس از جامد شدن هم چروک نمیشود. اما با همهی کاربردهایش، ناخالصی زیادی دارد و ۴ درصد آن کربن است. این کربن سختی بسیاری به چدن میدهد اما آن را شکننده هم میکند.
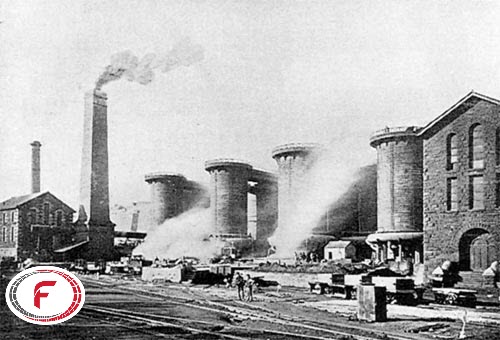
مرحلهی سوم: تولید فولاد
تکنیکهای تولید فولاد در زمان انقلاب صنعتی در قرن نوزدهم تا به امروز همواره در حال پیشرفت بوده است. البته مدلهای امروزی اغلب بر مبنای روش بسمیر هستند. یکی از مهمترین پیشرفتهای امروز این است که تولید فولاد نه تنها فقط از مادهی خام بلکه از راه بازیافت هم امکان پذیر شده است.
تولید اولیهی فولاد
دو پروسهی کلی برای انجام این کار وجود دارد:
- تولید فولاد مبنی بر اکسیژن (با کورههای اکسیژنی)
- کورهی قوس الکتریکی
در روش اول یک شمش فولاد بازیافت شده با آهن مذاب ترکیب میشود. در این زمان گاز اکسیژن در آن دمیده میشود. این کار سطح کربن را به مقدار ۰ تا ۱/۵ درصد کاهش داده و میزان فسفر و گوگرد را نیز کم میکند.
در روش کورهی قوس الکتریکی، فولادی که حدود ۹۰ درصد بازیافت شده است را در قوس الکتریکی به دمای ۱۶۵۰ درجه وارد میکنند. فلز ذوب میشود و آن را به فولاد درجه یک تبدیل میکنند.
تولید تکمیلی فولاد
در این نوع از تولید فولاد همزمان از اکسیژن و قوس اکتریکی برای آماده سازی فولاد استفاده میشود. این آماده سازی به وسیلهی کم و زیاد کردن عناصر مختلف، استفاده از دماهای مختلف و محیط تولید متفاوت انجام میشود.
ادامهی بهینهسازی فولاد
فولاد مذاب خنک میشود و آن را به یک ورق نازک تبدیل میکنند. این ورق وارد رولهایی شده، کامل خنک و جداسازی میشود. این فولاد را در ابعاد مورد نظر خود میبُرند تا در محل مناسب از آن در تولید استفاده شود. لوله، سیم و خیلی شکل های دیگر.
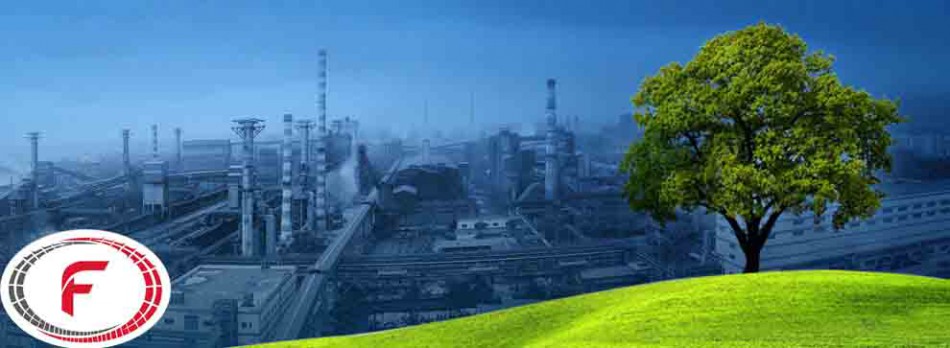
شکل دهی اولیه
فولاد بهینهسازی شده به شکلهای مختلفی درمیآید. این کار معمولاً به وسیلهی رول کردن داغ انجام میشود. در این فرآیند، نقصهای فولاد به طور کامل از بین میرود و به طور کامل به شکل مورد نظر در میآید. این محصولات رول شده میتوانند به شکل پهن، بلند، لوله و... در بیایند.
ساخت و تولید نهایی
شکل دهی ثانویه، فرم نهایی فولاد را به آن میدهد. این شکل دهی ثانویه شامل مراحل زیر میشود:
- شکل دهی (رول سرد)
- شکل دهی با ماشین
- اتصال - لایه نشانی (گالوانیزه کردن)
- مقاوم سازی دمایی
- رفع نقصهای سطحی
ادامه مطلب: تولید فولاد و ارتباط آن با محیط زیست (قسمت دوم)
به نقل از Greenspec.co.uk