آبکاری یا گالوانیزه کردن به عملیاتی گفته میشود که در طی آن پوشش روی بر روی سطح فلز قرار گرفته و مانع از خوردگی آهن و فولاد میشود. همراه ما باشید تا در این مقاله موارد ذیل را مورد بررسی قرار دهیم:
- آبکاری گالوانیزه سرد و گرم چیست؟
- تمیزکاری سطح برای گالوانیزه کردن
- چگونگی انجام عملیات گالوانیزه کردن
- دسته بندی فرآیند پوشش دهی ورق گالوانیزه در صنعت
- آبکاری گالوانیزه گرم چیست؟
- آبکاری گالوانیزه سرد چیست؟
- تفاوت گالوانیزه گرم و سرد
- کاربردهای عملیات گالوانیزه کردن
آبکاری گالوانیزه سرد و گرم چیست؟
آبکاری گالوانیزه سرد و گرم، گالوانیزه کردن یا گالوانیزاسیون به عملیاتی گفته میشود که طی آن فلز روی به عنوان پوششی محافظ، بر روی فلز زیرین که عمدتاً آهن و فولاد است، قرار میگیرد. آهن و فولاد، مواد جدایی ناپذیر از تکنولوژی و پیشرفت صنایع در زندگی مدرن این دوران هستند و تنها خطری که آنها را تهدید میکند، خطر خوردگی، زنگ زدگی و اکسید شدن است. برای مقابله با این خطرات، فلزات را گالوانیزه میکنند. برای گالوانیزه کردن فلزات از دو روش کلی گالوانیزه گرم و گالوانیزه سرد (الکترولیز) استفاده میشود. لایه گالوانیزه از فلز در برابر خوردگی و زنگ زدگی محافظت میکند.
گالوانیزه کردن (Galvanization) و به خصوص گالوانیزه گرم، قدیمی ترین و مهم ترین روش ایجاد پوشش روی است. سالانه بالغ بر ۲ میلیون تن روی بدین روش استفاده میشود، تا بر روی حدوداً ۴۰ میلیون تن فولاد پوشش داده شود. تمامی انواع فولادهای معمولی و چدنها را میتوان بدین روش پوشش داد، اما نوع پوشش ایجاد شده به عناصر آلیاژی بستگی دارد. نزدیک به نیمی از فولاد تولید شده در دنیا به صورت ورق و یک چهارم به صورت قطعات ساخته شده و بقیه به صورت لوله یا سیم است. گالوانیزه هر یک از چهار نوع محصول، صنعت جداگانهای را تشکیل داده است. به لحاظ متالورژیکی فرآیندهای گالوانیزه کردن قطعات ساخته شده و لولهها، مشابه یکدیگر است. اما در فرآیند مورد استفاده برای ورقها، مقدار کمی مواد افزودنی به روی اضافه میشود تا پوشش حاصل دارای مقدار کمتری آلیاژ روی – آهن باشد و در نتیجه بسیار انعطاف پذیر شود.
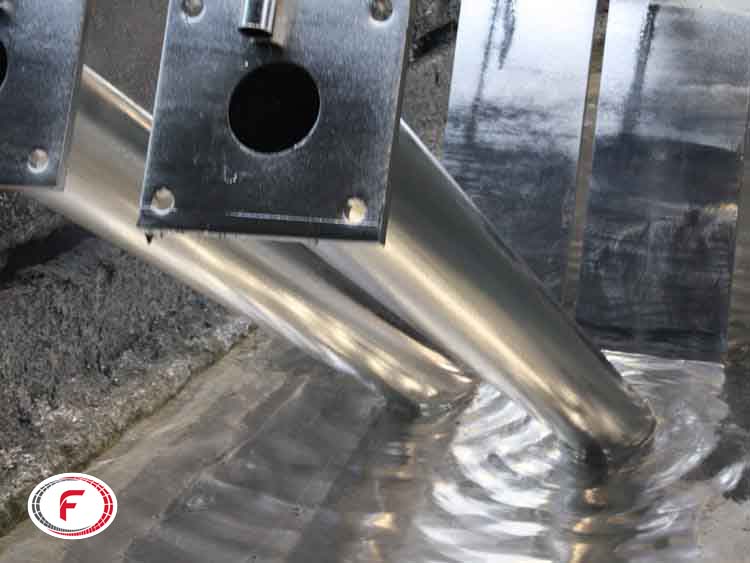
تمیز کاری سطح برای گالوانیزه کردن
روغنها، چربیها و صابونهایی که در حین عملیات ماشین کاری یا شکل دادن روی سطح فلز چسبیدهاند را باید با یک یا چند روش مانند چربی زدایی با بخار، تمیزکاری با حلالها یا امولسیونها و هم چنین محلولهای چربی گیری از بین برد. پس از مرحله چربی گیری، برای از بین بردن رسوبات و اکسیدهای سطحی، قطعات وارد مرحله اسید شویی میشوند، بدین منظور از محلولهای آبی اسید سولفوریک با اسید کلریدریک استفاده میشود. غلظت اسید کلریدریک مصرفی حدود ۱۰-۱۵ درصد است ولی دمای آن بین ۶۰ تا ۸۰ درجه سانتی گراد است. برای کوتاه کردن زمان اسید شویی میتوان از روش الکتریکی استفاده کرد. در این صورت در حمام اسید سولفوریک از آندهای سربی به همراه ولتاژ کم و چگالی جریان زیاد استفاده میشود. استفاده از این روش علاوه بر آنکه زمان عمل را ۱۰-۲۰ درصد کاهش میدهد، میزان مصرف اسید سولفوریک را نیز کم میکند.
بازار آنلاین خرید و فروش محصولات فولادی
چگونگی انجام عملیات گالوانیزه کردن
با فرو بردن قطعه فولادی یا آهنی تمیز درون مذاب روی، ابتدا روی در اطراف قطعه منجمد میشود، آنگاه با گرم شدن قطعه کار بر اثر انتقال حرارت مذاب به آن، این روی منجمد، مجدداً ذوب شده و بر اثر واکنش روی مذاب با سطح قطعه، آلیاژهایی از آهن و روی در سطح قطعه ایجاد میشوند و با خروج قطعه از داخل مذاب، مقداری از روی مذاب که به آن چسبیده از حمام خارج شده و یک لایه تقریباً خالص روی را در سطح خارجی پوشش ایجاد میکند.
در دمای معمولی حمام گالوانیزه، واکنش بین آهن و روی نسبت به زمان به صورت سهموی است یعنی سرعت انجام واکنش ابتدا سریع است، ولی با گذشت زمان این سرعت کاهش مییابد و اگر قطعه مدت طولانیتری درون مذاب قرار گیرد، ضخامت پوشش افزایش زیادی نخواهد یافت. در دامنه حرارتی ۴۸۰-۵۲۰ درجه سانتی گراد و یا در مورد برخی فولادهای ویژه (خصوصا فولادهای پرسیلیس) در دمای نرمال گالوانیزه (۴۵۰-۴۶۰ درجه سانتی گراد) واکنش بین آهن و روی نسبت به زمان به صورت خطی میباشد، یعنی ضخامت لایههای آلیاژی با افزایش زمان غوطه وری درون مذاب، افزایش یافته و واکنشها تقریبا با همان سرعت اولیه ادامه مییابند. در این حالت کنترل پوشش مشکل تر است.
عمل گالوانیزه کردن در دمای ۵۳۰ تا ۵۶۰ نیز مرسوم است که در این حالت پوشش نازکی کاملا آلیاژی به رنگ خاکستری فلزی ایجاد میشود. کاربرد این دما، بیشتر برای قطعات کار شده، مرسوم است. یکی از نکات بسیار مهم در عمل گالوانیزه، افزایش مینیمم وزن پوشش، با افزایش ضخامت قطعه فولادی است. این امر ناشی از تأثیرات زمان گرم شدن قطعه است.
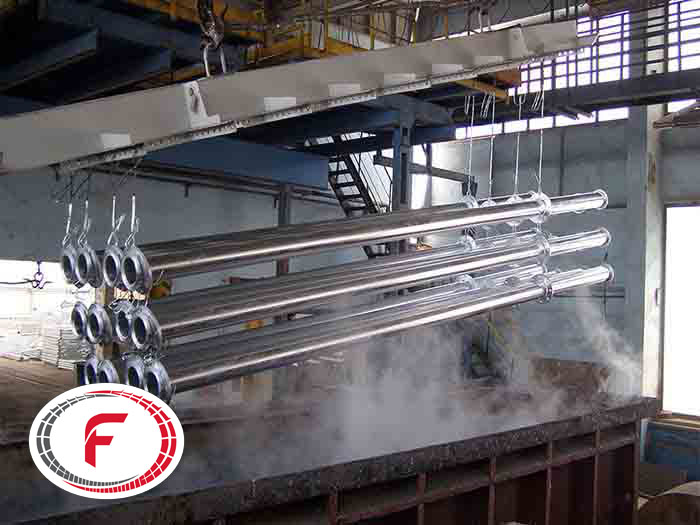
دسته بندی فرایند پوشش دهی ورق گالوانیزه در صنعت
این فرایند را در چند روش مختلف میتوان دسته بندی نمود. این روشها عبارتند از:
- سرد
- غوطه وری داغ
- پوشش دهی مکانیکی
- اسپری نمودن روی (متالایزینگ)
- رنگ کردن با خاک فلز روی
در روش تولید ورق گالوانیزه سرد از طریق الکترولیز نمکهای روی در داخل یک محلول آبی، هر قطعهای از قبیل ورقهای کویل شده یا کویل نشده پوشش داده میشوند. اصل این روش با استفاده از الکترولیت اسیدی نیز انجام میشود. در این روش ضخامت پوشش لایه روی ایجاد شده کمتر از ضخامت لایه روی در حالت غوطه وری گرم بوده و معمولاً در مصارف خانگی کاربرد دارد.
در روش غوطه وری ورق گالوانیزه گرم عملیات پوشش دهی از طریق عبور دادن مداوم ورق، سیم، لوله و یا هر مقطع دیگر از داخل حمام مذابی که ترکیبی از روی، منگنز، قلع، نیکل، مس و آلومینیوم و فسفر بوده است اتفاق میافتد. در این پروسه با دمش هوا میتوان ضخامت لایه روی را کنترل نمود. این روش خود نیز به دو نوع تقسیم میشود که شامل غوطه وری مداوم و غیر مداوم میباشد. در روش غیر مداوم ورقهای بریده شده را داخل حمام قرار میدهند ولی در روش مداوم، کویلهای پیوسته در یک خط ممتد مورد پوشش دهی قرار میگیرند.
پوشش دهی مکانیکی برای پوشش دهی قطعات ریز با اندازه ۳۰۰-۲۰۰ میلی متر و وزن کمتر از ۵۰ کیلوگرم استفاده میشود. عملیات پوشش دهی ورق گالوانیزه با این روش از طریق غوطه ور نمودن این قطعات در ترکیبی از پودر روی و ذرات شیشه انجام پذیر است. به این طریق که بعد از آماده سازی قطعات آنها را از طریق پاشش مس پوشانده، سپس در داخل یک بشکه جایگذاری کرده و بشکه را با ترکیب شیمیایی گفته شده پر نموده و آن را زیر و رو میکنند تا ذرات روی بتوانند بر روی قطعه بنشینند.
در روش اسپری روی، ابتدا روی را به صورت پودر به داخل یک تفنگ ریخته و سپس حرارت داده میشود تا پودر روی ذوب شده و سپس روی مذاب به روی قطعات مورد نیاز نشانده شود. به منظور پاشش روی مذاب، از هوای کمپرس شده و یا گازهای حاصل از احتراق برای تامین سرعت مناسب در پاشش استفاده میشود.
در روش رنگ کردن با روی، ابتدا سطح مورد نظر با سنگ ساییده شده، سپس لایه رنگ روی به روش پاشش و یا از طریق فرچه رنگ، روی سطح را میپوشاند. لایه فیلم تشکیل شده دارای ۹۵-۹۲ درصد روی در این روش خواهد بود.
آبکاری گالوانیزه گرم چیست؟
گالوانیزه گرم یکی از قدیمی ترین روشهای گالوانیزه کردن فلزات است که از حدود ۱۵۰ سال پیش تاکنون استفاده میشده است. در این روش قطعه فلزی مورد نظر را وارد محیطی حاوی روی مذاب با دمای ۴۶۰ درجه سانتی گراد میکنند تا قطعه کاملا در روی مذاب غوطه ور شود. پس از آن قطعه را از وان روی خارج میکنند، آنگاه لایه روی، با اکسیژن و کربن واکنش انجام داده و تبدیل به لایهای مقاوم در برابر خوردگی و زنگ زدگی میشود.همچنین پس از انجام گالوانیزه گرم، بین فولاد و روی مذاب نیز واکنش شیمیایی انجام شده و چندین لایه مرکب از آهن و روی، تشکیل میشود که از فلز پایه در برابر خوردگی و سایش و زنگ زدگی محافت میکند.
ضخامت لایه گالوانیزه در این روش بین ۱۰۰ تا ۱۳۰ میکرون است. ظاهر لایه روی در روش گالوانیزه گرم، مات و کدر و به رنگ توسی است و سطح یک نواخت و صافی ندارد.
آبکاری گالوانیزه سرد چیست؟
برای اینکه با آموزش آبکاری گالوانیزه سرد آشنا شویم باید بگوییم که در روش گالوانیزه سرد (الکترولیز) نمک روی را داخل محلول آبی یا اسیدی (الکترولیت) ریخته و به قطعه مورد نظر اسپری میکنند. ضخامت لایه گالوانیزه در این روش در حدود ۲۵ میکرون است. ظاهر لایه روی یا زینک در روش گالوانیزه سرد، براق و یکنواخت است.
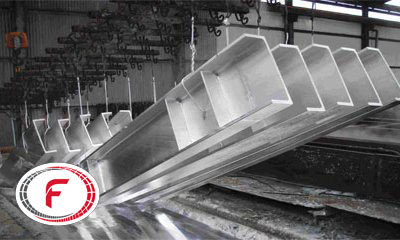
تفاوت گالونیزه گرم و سرد
- قطعاتی که به روش گرم، پوشش داده میشوند، بیشتر برای استفاده در محیط باز و فضای خارجی مناسب هستند. بنابراین مقاومت فلزاتی که با روش گرم گالوانیزه شدهاند، بسیار بیشتر از فلزاتی با روکش به روش سرد است.
- ضخامت لایه روی در روش گرم بیشتر و حدود ۱۰۰ تا ۱۳۰ میکرون است. در حالی که در روش سرد ضخامت لایه روی کمتر از ۲۵ میکرون است.
- پوشش روی در فلزات دارای لایه گرم، ظاهری مات و کدر و در فلزات دارای پوشش سرد ظاهری براق و درخشان دارند.
- با توجه به اینکه ضخامت لایه روی در سرد کمتر از گرم میباشد، درصورت بروز خراش بر روی سطح آن دچار زنگ زدگی و از بین رفتن لایه محافظ میشود.
کاربردهای عملیات گالوانیزه کردن
از روش سرد بیشتر برای پوشش دهی فلزاتی که مصارف بهداشتی دارند یا ورق و لولههایی با ضخامت کم و قطعات فلزی ریز استفاده میشود. همچنین در صنایع ساخت خودرو، پیچ و مهره، قطعه سازی و کابینت سازی نیز کاربرد دارد.
از روش گرم بیشتر برای پوشش دهی قطعات مورد استفاده در فضای باز به کار میرود. مثلا دکلهای مخابراتی، گارد ریل جادهها، دکلهای فشار قوی برق، لولههای آب با ضخامت بالا و تیرهای برق با این روش پوشش دهی میشوند تا در مقابل خوردگی و زنگ زدگی مقاوم باشند.
ضخامت لایه ایجاد شده در این روش بین ۱۰۰ تا ۱۳۰ میکرون است. ظاهر لایه روی در روش گرم، مات و کدر و به رنگ توسی است و سطح یک نواخت و صافی ندارد.
نکته مهمی که باید به آن اشاره کرد؛ برای اینکه روی کاملا به سطح فلز بچسبد و لایهای محافظ تشکیل دهد، لازم است که سطح فلز کاملا تمیز و عاری از هرگونه آلودگی و ناخالصی و زنگ زدگی باشد. بنابراین قبل از عملیات گالوانیزاسیون، فلزات را به روش اسید شویی، در محلولی اسیدی مانند اسید سولفوریک یا اسید کلریدریک به همراه ایجاد لرزش و حرکت غوطه ور میکنند تا هر گونه اضافات و آلودگی از سطح آنها پاک شود. سپس عملیات گالوانیزه گرم یا سرد را آغاز میکنند البته باید در نظر داشت که ورقهایی که در بازار به ورق گالوانیزه شهرت دارند هم با روشی تقریباً مشابه آبکاری گرم تولید میشوند.
با هم ببنیم ویدئو عملیات گالوانیزه کردن
تهیه شده در گروه تولید محتوای فولاد۲۴