گندله چیست؟
گُندله یعنی گلولههای تولیدشده از نرمه سنگآهن و سایر مواد افزودنی که نخست خام و سپس پختهشده و سخت میشود، و برای احیا به روش سنتی تولید آهن در کوره بلند و یا روشهای متعدد احیای مستقیم به کار میرود.
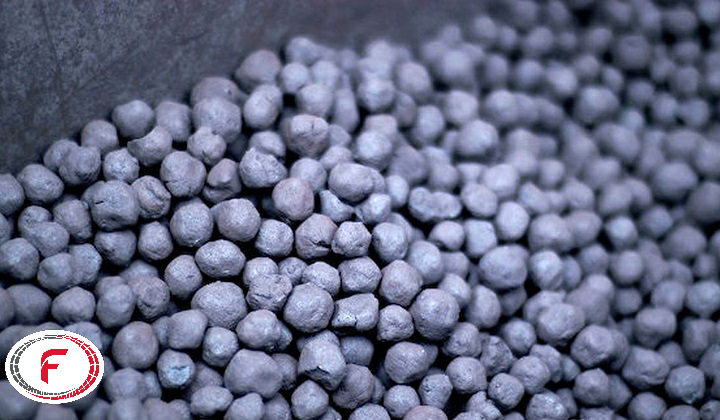
کنسانتره محصول کارخانه کانه آرائی است و بهصورت کانههای آهن دانهریزی است که به شکل فیزیکی قابلمصرف نیستند، این نرمهها، تراوایی گاز را در بار کوره بلند بهصورت ناموزون کاهش میدهند و عملکرد کوره بلند را مختل میکنند و همینطور در کارخانه احیا مستقیم نیز اشکالاتی را ایجاد مینمایند، بنابراین نرمههای آهن را بهصورت گندله درمیآورند که بهعنوان فرآورده میانی از معدن تا کورههای تولید آهن و فولاد در نظر گرفته میشود.
از آنجائی که گندلهها ماده اولیه به شمار میآیند، لذا باید در کورههای احیا ویژگی مکانیکی، شیمیایی و حرارتی مطلوبی را داشته باشند. گندلهها، گویهایی تولید شده از کنسانتره ها و کانههای طبیعی آهن هستند که با ترکیبات کانیشناختی و شیمیایی متفاوتاند. در واقع هدف واحد گندلهسازی تبدیل کنسانتره آهن به گندله آهنی با هندسه و تخلخل یکنواخت است.
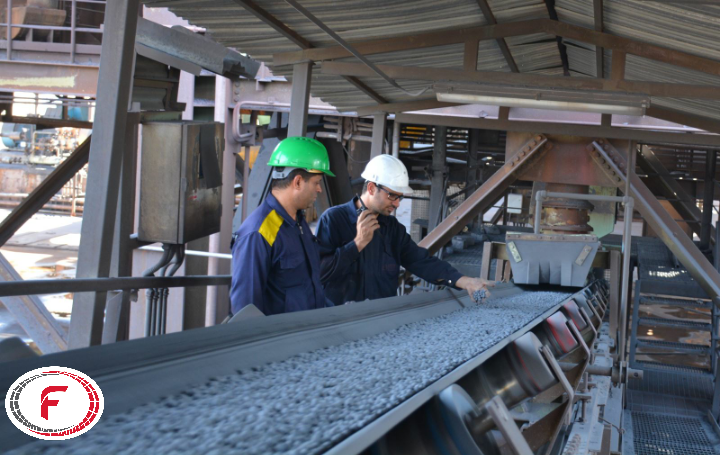
مواد اولیه گندلهسازی
سنگهای آهن
سنگآهن مهمترین مواد اولیه در روش های گندلهسازی بهحساب میآید. این ماده اولیه اغلب بهصورت کنسانتره حاصل از پر عیار کردن یا حذف مواد سنگی کانههای آهن در کارگاههای کانهآرایی میباشد. کنسانتره ها باید بر حسب نوع عملیات کانهآرایی مورد خردایش قرار گرفته و نرم میشود. در مواردی که خردایش انجامشده برای کانهآرایی بهمنظور گندلهسازی کافی نباشد باید مجدداً کنسانتره ها نرمتر شوند، بهطوریکه قسمت عمده ذرات سنگآهن به ابعاد زیر ۴۵ میکرون (معادل مش ۳۲۵) درآیند. کنسانتره ها اکثراً مرطوب بوده و حاوی حداقل ۱۰ درصد رطوبت میباشند. در برخی مواقع بهمنظور کاهش رطوبت کنسانتره، نرمههای سنگآهن خشک را با آن مخلوط میکنند.
مواد افزودنی
افزودنیهایی که در عملیات گندلهسازی به سنگآهن افزوده میشوند شامل: بنتونیت، آهک، هیدروکسید کلسیم، دولومیت، شیر آهک، سیمان و انواع مواد آلی است.
خواص گندلهها
- توزیع یکنواخت ابعاد بهطور عمده از ۹ تا ۶۱ میلیمتر
- تخلخل زیاد و یکنواخت ۵۲ تا ۰۳ درصد
- ترکیب کانیشناختی یکنواخت به شکل هماتیت یا ترکیبات هماتیت دار احیا شونده
- استحکام مکانیکی زیاد و یکنواخت
- مقاومت به سایش
- استحکام مکانیکی کافی حتی در برابر تنش گرمایی در محیطهای احیاکننده
- قابلیت چسبندگی کم داشته باشد
دیسکهای گندلهسازی
یکی از شایعترین روشهای گندلهسازی در تمامی کارخانجات روش گندلهسازی بهوسیله دیسک گندلهسازی است. در این روش مواد خام روی سطح دیسک دوار موردنظر پخته میشود و همزمان با حفظ رطوبت دستگاه عمل گندلهسازی نیز صورت میگیرد.
صرفا جهت اطلاع از: قیمت روز مواد معدنی کلیک کنید
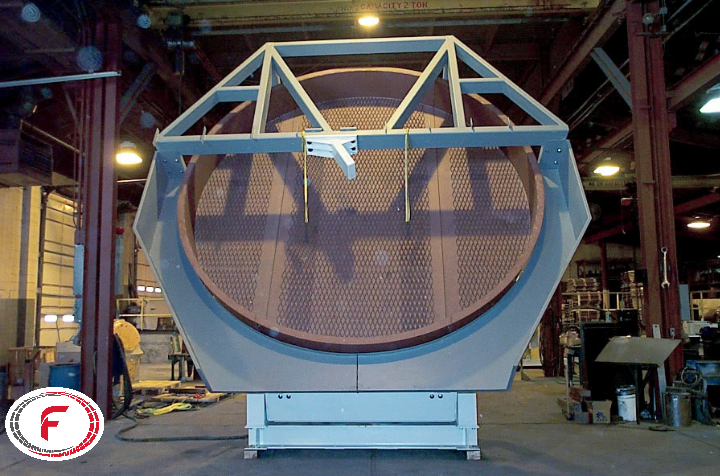
ویژگیهای دیسکهای گندلهسازی
- سرعت دوران (حدود ۳۰۰ تا ۱۵۰۰ دور در ساعت معادل ۵ تا ۲۵ دور در دقیقه)
- زاویه انحراف نسبت به افق و سیکل حرکتی گندلههای در حال شکل گیری
- تنظیم و تغییر خواص مکانیکی گندلهها
- اندازه یکسان گندلهها
عملیات گندلهسازی در دیسک
برای تولید گندله خام، نرمه سنگآهن که شامل مواد افزودنی است با محلولهای تر کننده مانند آب جهت دستیابی به شکل کروی، در دستگاههای گندله ساز به چرخش در آورده میشوند تا گندله خام تولید گردد. ممکن است در عملیات گندلهسازی مواد افزودنی و چسبنده مانند هیدروکسید کلسیم بهمنظور بالا بردن کیفیت و خواص متالورژیکی مکانیکی گندله به آن اضافه شود، در این مرحله گندله با ابعاد مطلوب و استحکام مکانیکی کافی تولید و جهت حملونقل تا دستگاه سخت کردن یا پخت ارسال میشود.
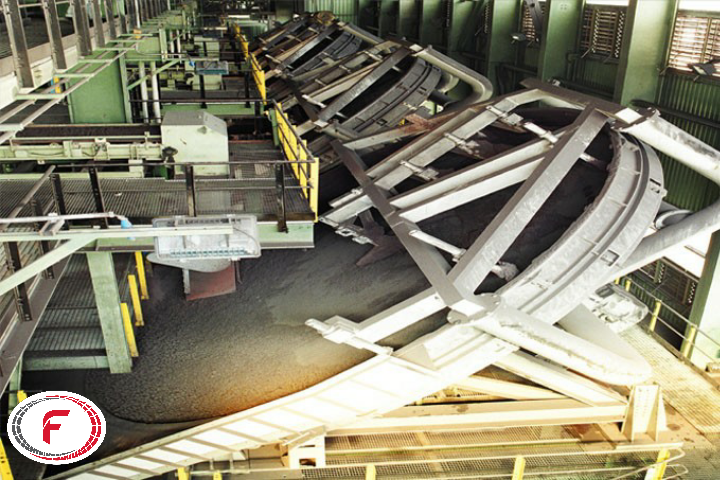
در مرحله دوم گندلههای خام، بهمنظور سخت شدن در اتمسفر اکسیدکننده بهدقت تا زیر دمای نرم شدن سنگآهن در دستگاهی حرارتی داده میشوند تا ابتدا خشک و سپس پخته شوند، این عمل باید به شیوهای صورت گیرد که درجه تخلخل آنها کاهش نیابد. سپس با پیوند بین ذرات سنگآهن و مواد دیگر بار گندله، ساختار بلوری سنگ تغییر مییابد و واکنشهایی بین مواد سرباره ساز و اکسیدهای آهن نیز انجام میشود. در این مرحله نخست مواد با یکدیگر مبادله شده و ترکیبات خنثی یا بازی بین دانههای اکسیدهای آهن تشکیل میشوند. در پایان مرحله پخت، سرد نمودن گندله داغ باید به صورتی انجام گیرد که ترکهایی در آنها ایجاد نشود.
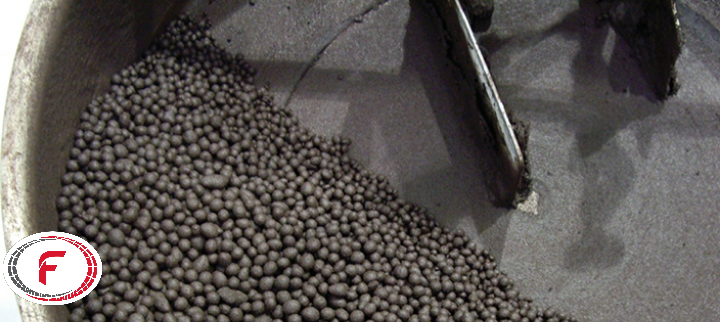
عوامل مؤثر در عملیات گندلهسازی
در عملیات گندلهسازی باید برای هر نوع مواد معدنی سرعت دوران دیسک و زاویه آن باید تنظیم گردد تا حداکثر سطح دیسک مورد استفاده قرار گیرد و مناسبترین شرایط گندله شدن به دست آید. هرگاه تحت شیب ثابت قطر دیسک افزایش یابد سرعت غلتیدن گندلهها و در نتیجه تراکم و استحکام آنها نیز افزایش خواهد یافت، اما اگر سرعت از حدی بیشتر شود بازده دستگاه کاهش حاصل خواهد کرد، لذا قطر دیسک و سرعت دوران آن را در مورد هر بار تنظیم نمود. این سرعت باید به صورتی تنظیم شود که نیروی گریز از مرکز وارد شده بر ذرات باعث پرتاب آنها از سطح صفحه دیسک به خارج نگردد.
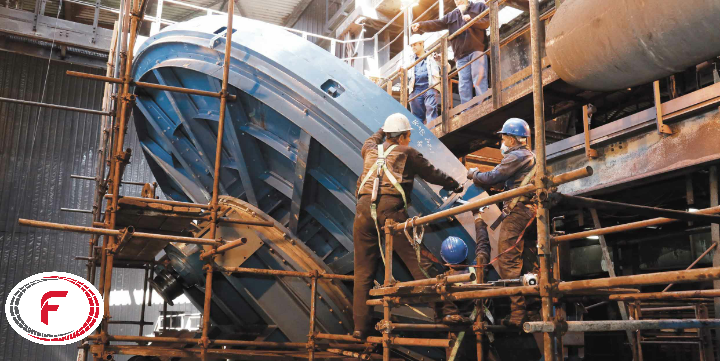
با افزایش سرعت دورانی در حد مجاز ظرفیت دستگاه نیز دچار کاهش میشود، به همین علت باید بین این دو عامل حد مناسبی انتخاب گردد. بالا رفتن سرعت دوران به علت نیروی گریز از مرکز باعث طولانیتر شدن زمان توقف گندله روی دیسک شده و بنابراین سرعت دوران دیسک در استحکام گندله نقش مهمی دارد.
عمل دیگر مؤثر در عملیات گندلهسازی در دیسک زاویه دیسک با افق است. هرقدر زاویه دیسک با افق کوچکتر باشد زمان غلتیدن ذرات از بالا به پایین در روی صفحه دیسک طولانیتر شده و در نتیجه گندله تراکم بیشتری حاصل میکند و مقاومتر میشود، ولی درعینحال ظرفیت کاهش خواهد یافت. در عملیات گندلهسازی یک قاعده کلی وجود دارد و آن این است که در هر نوع ماده معدنی با توجه به مشخصات فیزیکی آن ماده، اندازه ذرات و ابعاد گندله مورد تقاضا، سرعت دوران و زاویه شیب صفحه دیسک باید بهصورت صحیح تنظیم شود. قطر دیسک نیز در استحکام گندله اثر داشته و هر چقدر قطر آن بزرگتر باشد استحکام گندله بیشتر خواهد بود و گندله تراکم بیشتری خواهد یافت.
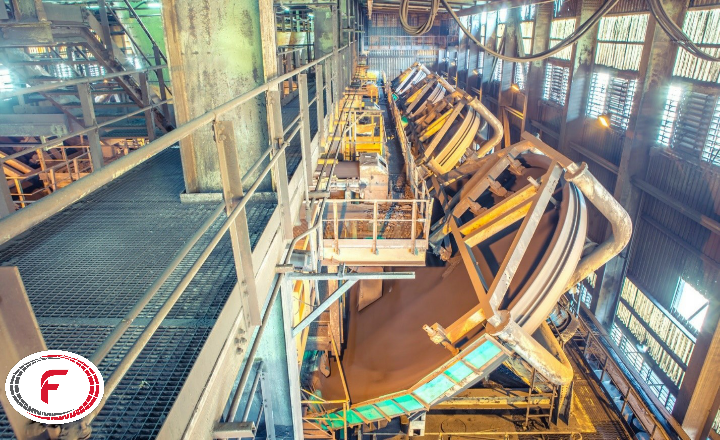
اجزا سیستم گندلهسازی
- سیستم انتقال مواد خام
- سیستم آسیاب و خردایش مواد اولیه
- واحد مخلوط سازی مواد اولیه
- تولید گندله خام
- کوره پخت گندله
- سیستم غبارگیر
- سیستم تامین آبخنک کننده
- سیستم انتقال محصول نهایی
- سیستم تصفیه آب
- سیستم تولید هوای فشرده
- آزمایشگاه
جهت مشاهده لیست تامین کنندگان مواد معدنی به وب سایت فولاد ۲۴ مراجعه نمایید.
منبع: گروه تامین محتوای فولاد ۲۴