FMEA چیست؟
FMEA (Failure Modes & Effects Analysis) ابزاري است که با کمترین ریسک، براي پیشبینی مشکلات و نقصها در مراحل طراحی و یا توسعه فرایندها و خدمات در سازمان به کار میرود. یکی از عوامل موفقیت FMEA زمان اجراي آن است. این تکنیک براي آن طرحریزیشده که یک اقدام قبل از واقعه باشد، نه یک تمرین بعد از آشکار شدن مشکلات. به بیانی دیگر، یکی از تفاوتهای اساسی FMEA با سایر تکنیکهای کیفی این است که FMEA یک اقدام کنشی و پیشگیرانه است، نه واکنشی. در بسیاري از موارد وقتی با مشکلی مواجه میشویم، ممکن است براي حذف آن اقدامات اصلاحی تعریف و اجرا شود.این اقدامات ، واکنشی در برابر آنچه اتفاق افتاده است.
در چنین مواردي حذف همیشگی مشکل، به هزینه و منابع زیاد نیاز دارد، زیرا حرکت از وضعیت موجود به سمت شرایط بهینه اینرسی زیادي خواهد داشت، اما در اجراي FMEA با پیشبینی مشکلات بالقوه و محاسبه میزان ریسکپذیری آنها، اقداماتی در جهت حذف و یا کاهش میزان وقوع آنها تعریف و اجرا میشود.این برخورد پیشگیرانه کنشی است در برابر آنچه ممکن است در آینده رخ دهد و مسلماً اعمال اقدامات اصلاحی در مراحل اولیه طراحی محصول یا فرایند، هزینه و زمان بسیار کمتري در بر خواهد داشت.
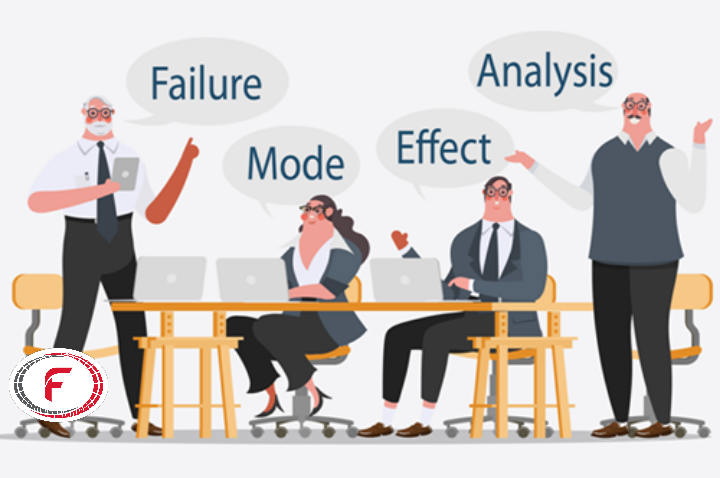
علاوه بر این، هر تغییري در این مرحله بر روي طراحی محصول یا فرایند بهراحتی انجامشده و درنتیجه احتمال نیاز به تغییرات بحرانی در آینده را حذف میکند یا کاهش خواهد داد.
اگر FMEA درست و بهموقع اجرا شود، فرایندي زنده و همیشگی است. یعنی هر زمان که قرار است تغییرات بنیادي در طراحی محصول و یا فرایند تولید (یا مونتاژ) انجام گیرد، باید بهروز شوند و لذا همواره ابزاري پویا است که در چرخه بهبود مستمر به کار میرود. هدف از اجراي FMEA جستجوي تمام مواردي است که باعث شکست یک محصول یا فرایند میشود، قبل از اینکه آن محصول به مرحله تولید برسد و یا فرایند آماده تولید شود.
تاریخچه
این تکنیک اولین بار در سال ۱۹۴۹ توسط ارتش امریکا مورداستفاده قرار گرفت و اولین کاربرد رسمی این روش در صنایع هوایی بوده است .این روش اولین بار بهعنوان ابزاري براي پیشگیري از اشتباهات و خطاهاي غیرقابلجبران مطرح گردید .این تکنیک جزو استانداردهاي نظامی بوده و تحت عنوان STD۱۶۲۹-MIL شناخته میشود.

FMEA یک تکنیک مهندسی بهمنظور مشخص نمودن و حذف خطاها ، مشکلات و اشتباهات بالقوه موجود در سیستم ، فرایند تولید و ارائه خدمات ، قبل از وقوع آن است. این روش میکوشد تا حد ممکن خطرات بالقوه موجود در محدودهاي که در آن ارزیابی ریسک انجام میگیرد و نیز علل و اثرات مرتبط با آن خطرات را شناسایی و اولویتبندی نماید و سپس به حداقل برساند .
مزایاي انجام FMEA
- ابزار مناسبی جهت پیشگیري از بروز خطرات است .
- روش مناسب کمی براي ارزیابی ریسک است .
- روشی مطمئن براي شناسایی خطرات ناشی از دستگاهها، تجهیزات و ماشینآلات است.
مراحل انجام FMEA
- جمعآوری اطلاعات
- شناسایی خطرات ( ایمنی + بهداشت حرفهای )
- تعیین اثرات هر خطر
- تعیین علل هر خطر
- بررسی اقدامات کنترلی موجود
- تعیین ضریب شدت
- تعیین ضریب احتمال وقوع
- تعیین ضریب کشف خطر
- ریسک اولویت عدد محاسبه ( RPN= Risk Priority Number )
- تصمیمگیری در خصوص پذیرش ریسک
- ارائه اقدامات اصلاحی پیشنهادي براي ریسکهای غیرقابلقبول
- محاسبه مجدد RPN = ریسک باقیمانده
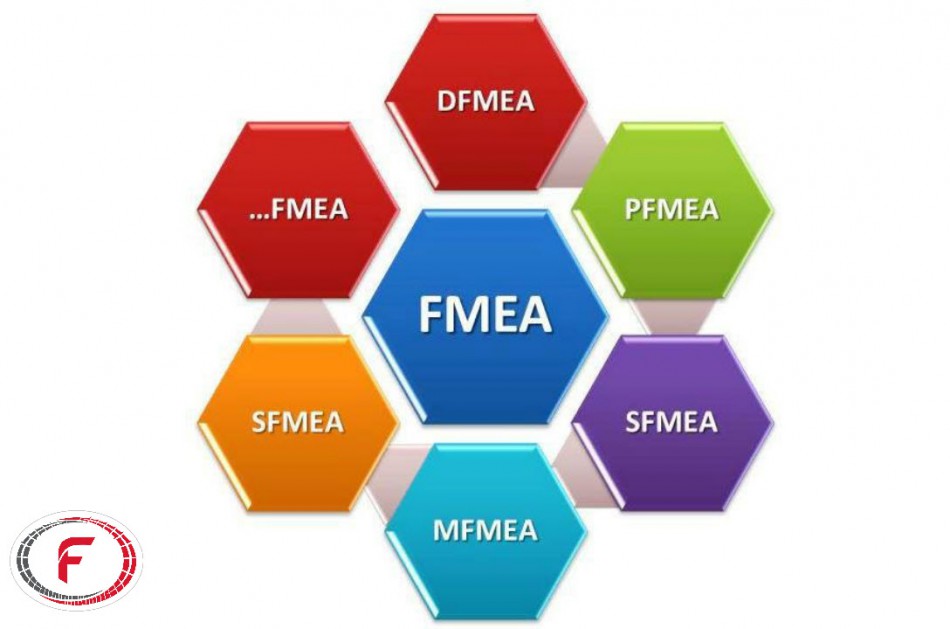
FMEA در چه شرایطی اجرا میشود؟
- در زمان طراحی سیستمی جدید، محصولی جدید و یا فرایندي جدید.
- زمانی که قرار است طرحهای موجود یا فرایند تولید/مونتاژ اجرا شود.
- زمانی که فرایندهاي تولید و یا مونتاژ و یا یک محصول در محیطی جدید و یا شرایط کاري جدید قرار میگیرد.
تکمیل FMEA
بهمنظور تکمیل FMEA تیم باید براي سؤالات زیر پاسخهای کاملی تهیه کند:
- حالات خرابی چه تأثیری بر مشتري خواهند داشت؟
- اثر خرابی چه شدتی دارد؟(عدد شدت)
- علل بالقوه خرابی کدماند؟
- احتمال وقوع علل خرابی چقدر است؟ (عدد وقوع)
- قدرت تشخیص کنترلهای موجود چه میزان است؟ (عدد تشخیص)
- در حال حاضر چه کنترلهایی بهمنظور پیشگیري و یا تشخیص حالات خرابی و علل آن انجام میشود؟
- تحت چه شرایطی محصول نمیتواند اهداف و مقاصد طراحی را برآورده سازد و یا نیازهاي فرایند تحقق نمییابد؟
- میزان خطرپذیری حالات بالقوه خرابی به ازاي علل مختلف چه مقداراست؟ (محاسبه RPN ) منظور از عدد RPN یا Number Priority Risk ، نمره اولویت ریسک است.
تشخیص × وقوع × شدت= RPN نمره اولویت ریسک
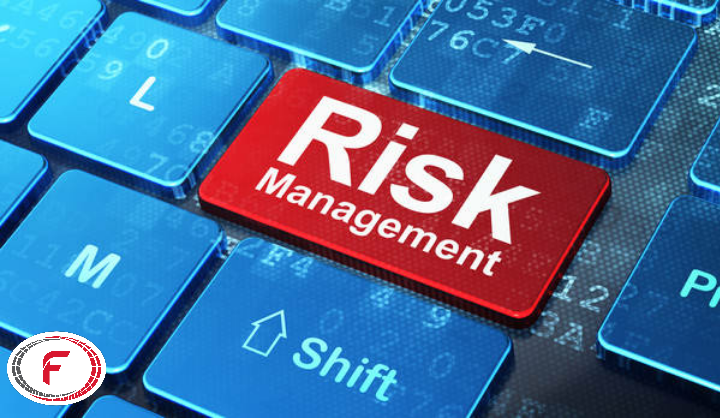
افزایش رقابت، افزایش توقعات و تقاضاهاي مکرر مشتري و تغییرات سریع فناوري، باعث افزایش سریع تعهدات تولیدکنندگان امروزي شده است و هر کمبود و انحرافی در عملکرد محصول، باعث از دست دادن بازار میشود. این عوامل موجب شده که امروزه سازمانها به استفاده از این تکنیک رویآورند تا به کمک آن مطمئن شوند محصولی بیعیب و قابلرقابت روانه بازار میکنند.
منبع: گروه تامین محتوای فولاد ۲۴