هنر جوشکاری برای انواع ورق شیوه خاص خود را دارد و مستلزم داشتن مهارت کافی است. جوشکاری ورق گالوانیزه به دلیل روکش جنس روی و ضخامت آن بسیار حساس است. در ادامه به توضیح این نوع جوشکاری می پردازیم.
در این مقاله به نکات ذیل اشاره شده است:
- نکات جوشکاری ورق گالوانیزه
- شیوه های جوشکاری انواع ورق گالوانیزه
- روش به حداقل رساندن ترک هنگام جوشکاری
- نحوه جوشکاری ورق گالوانیزه
نکات جوشکاری ورق گالوانیزه
در هنگام جوشکاری ورق گالوانیزه بالاخص ورق های گالوانیزه که دارای سطحی نسبتاً نازک تر نسبت به سایر قطعات فولادی هستند باید از الکترودهایی با سرعت بالا استفاده نمود. در صورت وارد نمودن گرمای زیاد به سطح ورق ممکن است حفره هایی روی سطح ورق پدیدار گردد از طرفی کیفیت جوش کاهش یافته انرژی نیز اتلاف می گردد.
حین جوشکاری موادی مانند گاز یا کف ایجاد می شود. روش هایی مانند حرارت دهی، برش، قوس پلاسما، هوا یا سوخت های اکسیژن دار را می توان به منظور حذف گاز و کف تولید شده به کار برد.
در جوشکاری ورق گالوانیزه پوشش روی، تبخیر شده و گاز ایجاد شده بسیار سمی می باشد. باید در حین عملیات از ماسک، عینک محافظ چشم، لباس ضد اشتعال، کلاه ایمنی و کفش عایق و سبک استفاده شود. زمان انجام کار و محل آن باید مخصوص باشد. برای این کار باید از الکترود متناسب با ضخامت ورق و همچنین دستگاه جوش مناسب استفاده شود.
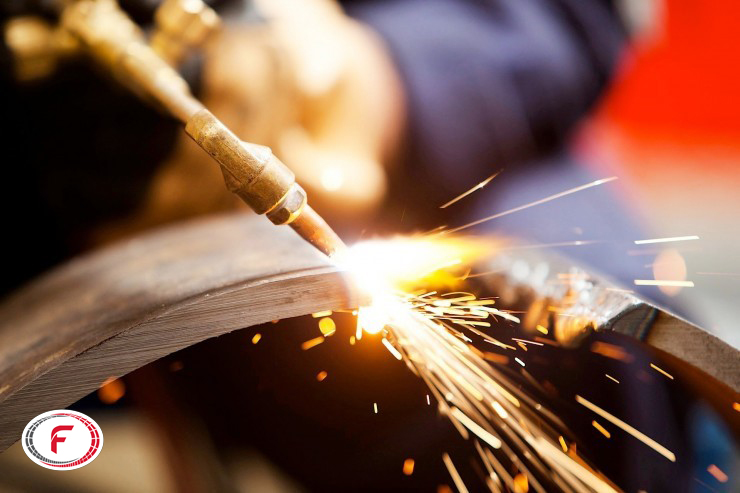
شیوه های جوشکاری انواع ورق گالوانیزه
در جوشکاری ورق گالوانیزه از روش های متداولی همچون جوشکاری لیزری، جوشکاری ذوبی و جوشکاری مقاومتی استفاده می شود. جوش مقاومتی به دلیل آسیب کمی که به پوشش ورق وارد می کند و دوامی که در برابر خوردگی و فرسایش دارد نسبت به بقیه روش ها بیشتر مورد استفاده قرار می گیرد.
الکترود جوشکاری ورق گالوانیزه
به سیم روکش دار که به وسیله آن عملیات جوش کاری انجام می شود و از جنس آلومینیوم، فلز ضد زنگ، نیکل و ترکیبات کربن می باشد الکترود جوشکاری می گویند. جوشکاری ورق گالوانیزه مانند بقیه فلزات انجام می شود با این تفاوت که تبخیر روی باعث ایجاد تخلخل در جوش می شود. در این جوش الکترود با سرعت بالا استفاده می شود و مقدار گوگرد الکترود نباید از ۸۵ درصد بیشتر باشد. در صورتی که مقدار گوگرد زیاد باشد فلز روی به داخل فلز جوش نفوذ پیدا کرده و باعث ایجاد ترک می شود.
در صورتی که روی در حین جوشکاری بخار شده و از فلز جوش خارج شود، احتمال ترک کاهش خواهد یافت. به همین دلیل درز جوش با فاصلهی ریشهی بیشتر در این مواقع بهتر است. به عنوان مثال، بیشترین مشکل در اتصالات T شکل به دلیل حبس روی در سطح اتصال دو ورق ایجاد می شود. این مشکل را می توان با طراحی مناسب برطرف ساخت.
در جوش با گاز آرگان الکترود باید سایز متوسط داشته باشد و از دستگاه خوبی استفاده شود. حداکثر ضخامت در نظر گرفته شده برای این دسته از الکترودها چیزی حدود ۲٫۵ میلی متر و جریان نیز ما بین ۱۰ الی ۲۰۰ آمپر در نظر گرفته می شود. هر چه سرعت کار بالاتر باشد متقابلاً کیفیت نقطه جوش نیز مطلوب تر خواهد بود.
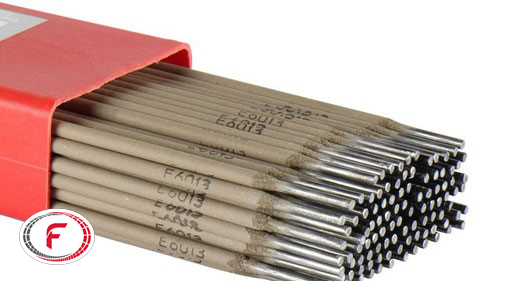
روش به حداقل رساندن ترک هنگام جوشکاری
- ایجاد یک شیب حداقل ۱۵ درجه و استفاده از درز جوش با پخ یک طرفه یا دو طرفه
- حذف پوشش در ناحیه ی اتصال از یک یا هردو سطح به وسیله ی سوزاندن روی سنگ زنی و …
- ایجاد یک فضای حداقل ۱/۶ میلی متری جهت ایجاد فضای مناسب برای خروج بخار
- انتخاب صحیح مواد مصرفی
نحوه جوشکاری ورق گالوانیزه
اولین نکته ای که باید به آن دقت کرد انتخاب جریان برق مناسب است که باید متناسب با الکترود مورد نظر و بین ۳۵ تا ۴۰ درجه سانتی گراد باشد. بعد از انتخاب صحیح جریان الکتریکی هر دو لبه ی کار که قصد اتصال آن است روبروی یکدیگر قرار داده، اکنون الکترود را در جای مناسب تعبیه کرده و عملیات جوشکاری را با رعایت تمامی موارد ایمنی شروع می کنند. در پایان عملیات، الکترودهای جوشکاری توسط پودرهایی پوشش داده می شوند.
این پوشش متناسب با کاربرد آن به پوشش قلیایی، سلولوزی، اسیدی و روتیلی با ضخامت های مختلف تقسیم می شود. درمواقعی که نوع پوشش دارای حساسیت نیست از پوشش اسیدی به دلیل ارزان بودن و کیفیت پایین آن استفاده می شود. پوشش سلولوزی کیفیت بهتری دارد اما یکی از معایب آن مقاومت کم در برابر رطوبت است.
در پایان باید گفت که ورق گالوانیزه باید در محیط مناسب جوش داده شود و با وجود اینکه می توان بسیاری از تکنیک های جوش را برای آن استفاده نمود، باید با تاثیرات فرآیندهای جوشکاری مختلف بر ورقهای گالوانیزه آشنا بود و علاوه بر کنترل این تاثیرات، از اقدامات تعمیری پس از جوش بهره برد. همچنین نواحی تعمیر شدهی فولاد گالوانیزه، بیشتر در معرض خطر خوردگی بوده و بنابراین این نواحی باید زودتر از بقیهی سازه، مورد بازرسی قرار گیرند.