جوشکاری زیر پودری یا SAW
جوش زیر پودری یک فرایند جوش قوس الکتریکی است که در آن گرمای لازم برای جوشکاری توسط یک یا چند قوس بین یک فلزپوشش نشده، یک یا چند الکترود مصرفی و یک قطعه کار تامین می شود. در این روش نوک الکترود داخل پودری از مواد معدنی ویژه قرار می گیرد و قوس در زیر این پودر در امتداد مسیر جوشکاری تشکیل می شود. در این روش قوس قابل مشاهده نیست. در سیستم زیر پودری از سیم بدون روکش استفاده می شود، طوری که سیم به طور متوالی از قرقره مخصوص رها می گردد و ضمن تشکیل قوس نقش واسطه اتصال را نیز بر عهده دارد. قوس توسط لایه ای از فلاکس پودری قابل ذوب شدن که فلز جوش مذاب و فلز پایه نزدیک اتصال را پوشانده و فلز جوش مذاب را از آلودگی های اتمسفر حفاظت می کند، پوشیده می شود.
با پیشروی عملیات جوشكاری، علاوه بر هر لایه جوش، لایهای از سرباره دانه بندی شده ناشی از پودر محافظ نیز بر روی فلز جوش تشكیل شده و منجمد میشود. این سرباره بایستی كاملاً بر روی سطح جوش زدوده شود و در اغلب موارد به دور ریخته شود. اگر چه روشهایی برای استفاده مجدد و یا تركیب بخشی از سرباره استفاده شده با سربارههای جدید وجود دارد. در بعضی موارد، آنجایی كه سرباره بایستی كاملاً تمیز باشد، استفاده مجدد از پودرهای محافظ توصیه نمیشود. از آنجایی كه در روش زیر پودری از الكترودها و پودرهای جداگانه استفاده میشود، تركیبات گوناگونی از پودر و سیم جوش برای كاربردهای خاص ایجاد میشود. بطور كلی دو نوع تركیب برای پودر و سیم جوش وجود دارد:
- الكترود آلیاژی با پودر خنثی
- الكترود از جنس فولاد ساده كربنی با پودر آلیاژی
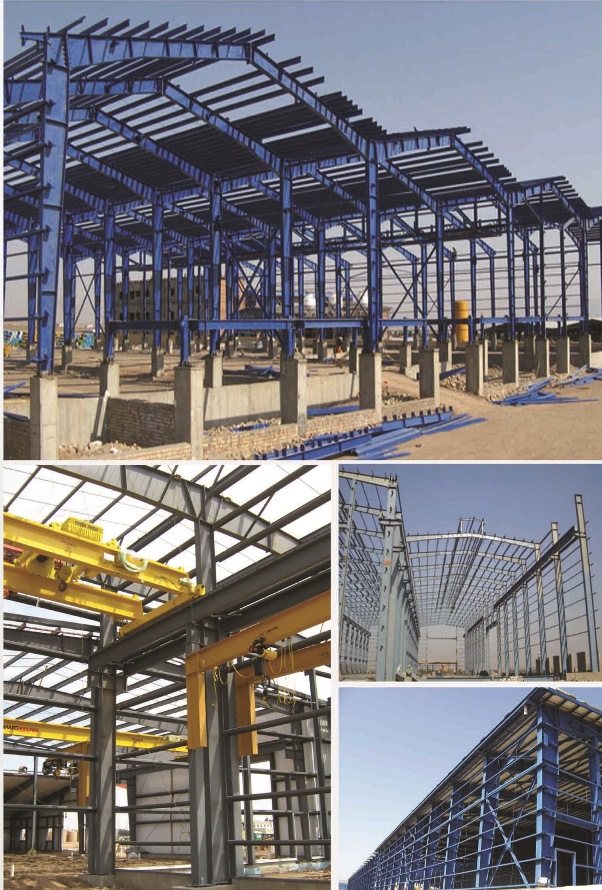
چگونگی انجام جوشکاری زیر پودری
در جوشکاری زیر پودری، انتهای سیم جوش داخل مواد روانساز قرار می گیرد. مواد روانساز منطقه ای که قرار است جوش شود، را می پوشاند. پیش از انجام جوشکاری یک لایه نازک از پودر فلاکس در سطح قطعه کار قرار می گیرد. قوس در امتداد خط اتصال حرکت می کند. پس از انجام جوشکاری پودر اضافی به یک قیف نگهدارنده برگردانده می شود. لایه های سرباره ذوب شده باقی مانده بعد از جوشکاری را می توان به راحتی از بین برد. هنگامی که قوس به طور کامل با لایه فلاکس پوشیده می شود، اتلاف حرارت به شدت کاهش می یابد. این امر یک راندمان حرارتی بالا به میزان ۶۰٪ فراهم می کند.
جوشکاری زیر پودری میتواند به ۳ روش نیمه خودکار، خودکار و ماشینی انجام گیرد. در روش نیمه خودکار جوشکاری زیر پودری، از تفنگ جوشکاری دستی استفاده می شود. تفنگ در این روش، وظیفه انتقال الکترود و پودر محافظ را دارد. تغذیه سیم جوش به صورت خودکار بوده و پودر محافظ تحت اثر نیروی گرانش از مخزن با ته مخروطی یا تحت فشار هوا توسط شیلنگ به محل اتصال، انتقال مییابد. در روش خودکار جوشکاری زیر پودری، جوشکاری بدون دخالت کاربر و توسط دستگاه جوشکاری و کنترل کننده های خودکار انجام میشود. روش جوشکاری زیر پودری ماشینی، توسط ماشین انجام می شود. کاربر در این روش شروع کننده جوشکاری است، آن را نظارت می کند و تنظیم متغیر های جوشکاری و سرعت جوشکاری را بر عهده دارد. همچنین کاربر تصمیم گیرنده زمان انتهایی جوشکاری است.
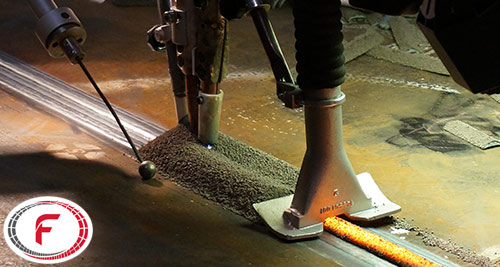
پودرهای جوشکاری زیر پودری
پودرهای جوشکاری مواد معدنی و یا فلزی دانه بندی شده ای هستند که در جوشکاری زیر پودری وظایفی نظیر رسانایی طول قوس، تشکیل پوشش سرباره، انجام واکنش های سرباره و در نهایت اکسیژن زدایی از مذاب را بر عهده داشته و در حقیقت نقش روکش الکترود را در فرایند دستی ایفا می کنند. شکل ظاهر گرده جوش تحت تاثیر عناصر شیمیایی پودر می باشد و دانه بندی پودر هم نقش مهمی را ایفا می نماید. باید توجه شود که یک پودر عمومی که بتواند روی اکثر فولادها ودرزها کاربرد داشته باشد وجود ندارد و بر پایه جنس و نوع کاربرد باید نوع پودر انتخاب شود. حداکثر میزان آمپر مصرفی را معمولاً پودر در حال مصرف مشخص می نماید. پودرهای جوشکاری شامل انواع اسیدی، معمولی و قلیایی می باشد. پودرهای جوشکاری به پودرهای جوشکاری پیش ذوب شده و پودرهای جوشکاری آگلومره تقسیم می شود:
پودرهای جوشکاری پیش ذوب شده توسط ذوب کردن مخلوطی از مواد اولیه که کاملاً آسیاب شدهاند به دست میآیند. محصول ذوب شده تحت فرآیند سرد کردن، سنگشکنی و الک کردن قرار گرفته و به دانهبندی مطلوب میرسد. استحکام و چگالی این دانه ها بالا بوده و در حین جابجایی امکان خاکه شدن آنها وجود ندارد. پودرهای پیش ذوب شده در برابر نفوذ اکسیژن و هیدروژن و بروز ترک هیدروژنی از خود مقاومت نشان می دهند و از این رو قابل استفاده در محیط های باز و بدون مسقف و مناطق مرطوب می باشند.
پودرهای جوشکاری آگلومره شده با اختلاط خشک چند ماده خام که کاملاً آسیاب شدهاند، تولید میشود. مواد چسبنده از قبیل سیلیکاتهای سدیم و پتاسیم به مخلوط اضافه شده و خمیر مخلوط برای تشکیل دانههای کوچک، آلگومره میشود. سپس این پودر در دمای ۸۰۰-۶۰۰ پخته میشود. چون دامنه دمای پخت زیر دمای واکنش مواد است، امکان استفاده از اکسیژنزداها و فروآلیاژها وجود دارد. علیرغم بالاترین هزینه تولید پودرهای جوشکاری آلگومره شده، مقدار مصرف این پودر در حین جوشکاری به دلیل چگالی حجمی کمتر، پایینتر است.
محدودیتهای جوشکاری زیر پودری
- تجهیزات پیچیده و گران
- در کاربردهای خاص شدیداً به مسطح بودن وضعیت جوشکاری محدود است، زیرا مسطح بودن و افقی بودن وضعیت، برای جلوگیری از ریختن فلاکس لازم است.
- پودر جوش ممکن است به آلودگی هایی آغشته شود که باعث تخلخل در جوش شوند.
- جدا شدن سرباره از جوش در برخی موارد به سختی صورت می گیرد.
- در جوش های چند پاسه، پس از هر عبور باید سرباره جوش برداشته شود تا از باقی ماندنش درون فلز جوش جلوگیری شود.
تجهیزات جوشکاری زیر پودری
تجهیزات لازم برای اجرای جوش زیر پودری (SAW) عبارتاند از:
- مولد
- مخزن پودر
- نازل پودر
- انبر
- سیستم نگهداری و هدایت الکترود لخت
- روبات هدایت انبر و ریلهای مربوطه
مزایای جوشکاری زیر پودری:
- جوشکاری بدون دود و تشعشع انجام می شود.
- بینیازی از جوشکار ماهر
- جوشکاری با سرعت بالا
- رسوب الکترود با بازدهی بالا
- جوش با سطح هموار و بدون پاشش قطرات مذاب
- نرخهای رسوب بالا
- عمق نفوذ جوش زیاد
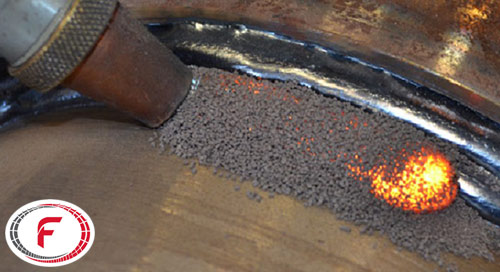
کاربرد جوشکاری زیر پودری
- جوشکاری مخازن تحت فشار
- خطوط لوله
- مخازن ذخیره
- سازه های سنگین
- کشتی سازی
- ساخت واگن های راه آهن
- ساخت تیر برق
موارد استفاده جوشکاری زیر پودری:
روش جوشکاری زیر پودری در بسیاری از صنایع و برای اتصال بسیاری از فلزات قابل كاربرد است. به دلیل نرخ رسوب نشانی بالای این روش، برای لایه گذاری و انجام ترمیمهای سطحی بسیار مناسب است. در شرایطی كه افزایش مقاومت به خوردگی سطحی و مقاومت به سایش مورد نیاز است، این روش كاملاً مقرون به صرفه و مورد اطمینان است. شاید مهمترین مزیت روش زیر پودری را بتوان در نرخ رسوب بالای آن خلاصه كرد. این روش راندمان بسیار بالاتری نسبت به سایر فرایندهای متداولتر دارد. روش زیر پودری محافظت بالایی را برای اپراتور تامین مینماید. چرا كه در حین جوشكاری هیچ قوس قابل رویتی وجود ندارد و بنابراین اپراتور میتواند كنترل جوش را بدون اینكه نیاز به استفاده از لنزهای فیلتر یا لباسهای محافظ سنگین داشته باشد، به عهده بگیرد.
یكی دیگر از دلایلی كه منجر به استفاده گسترده از این روش میشود قابلیت نفوذ بالای آن است. عمدهترین محدودیت روش زیر پودری در این است كه فقط در موقعیتهایی قابل اجرا است كه پودر محافظ مطابق طرح اتصال بتواند وظیفه خود را بدرستی انجام دهد (وضعیت تخت و افقی). در سایر وضعیتهای جوشكاری، برای اجرای مناسب این روش، نیازمند بكارگیری تجهیزات جانبی هستند.
تهیه شده در گروه تولید محتوای فولاد ۲۴